AI-Powered multi-purpose robotic stacking solution
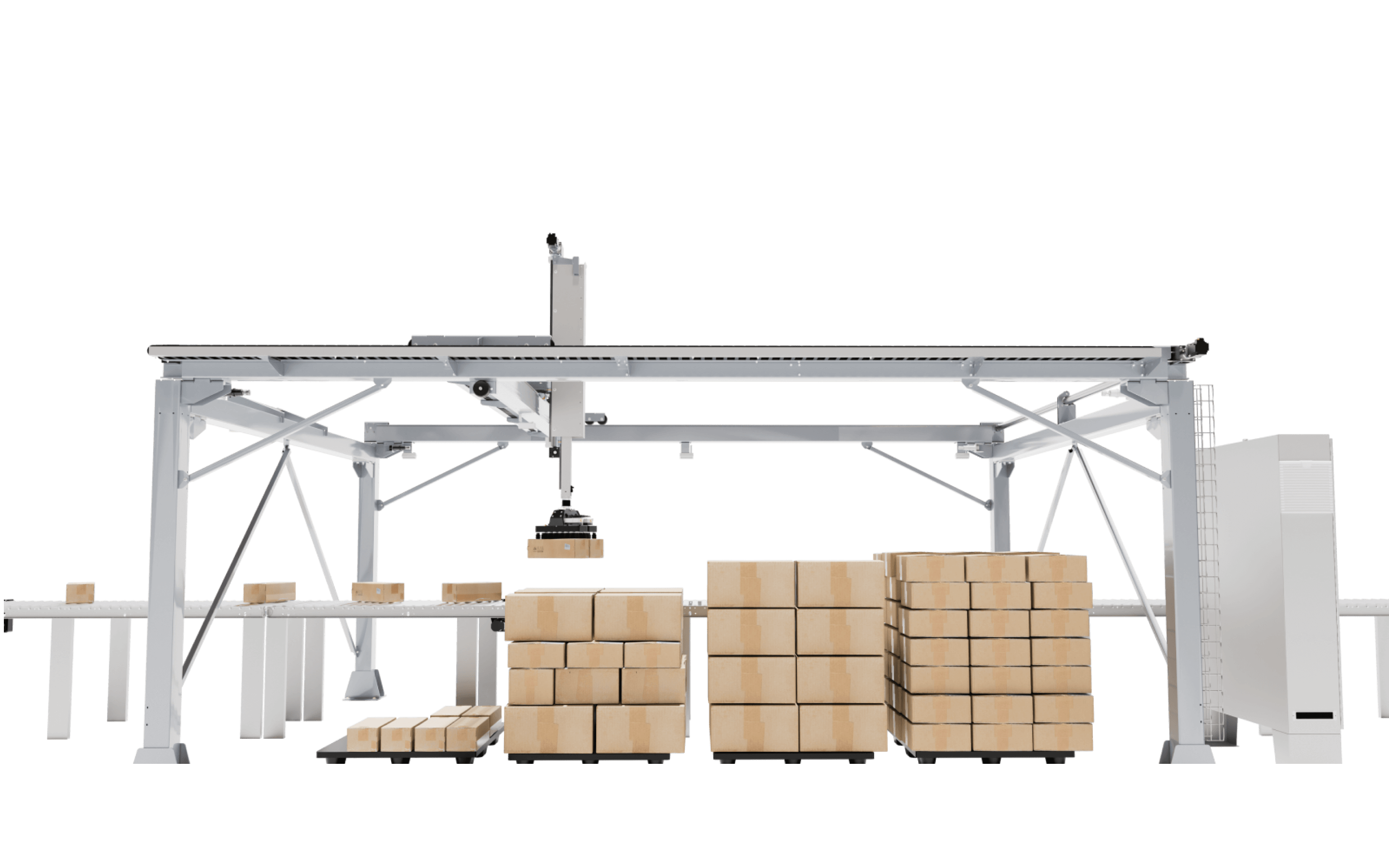
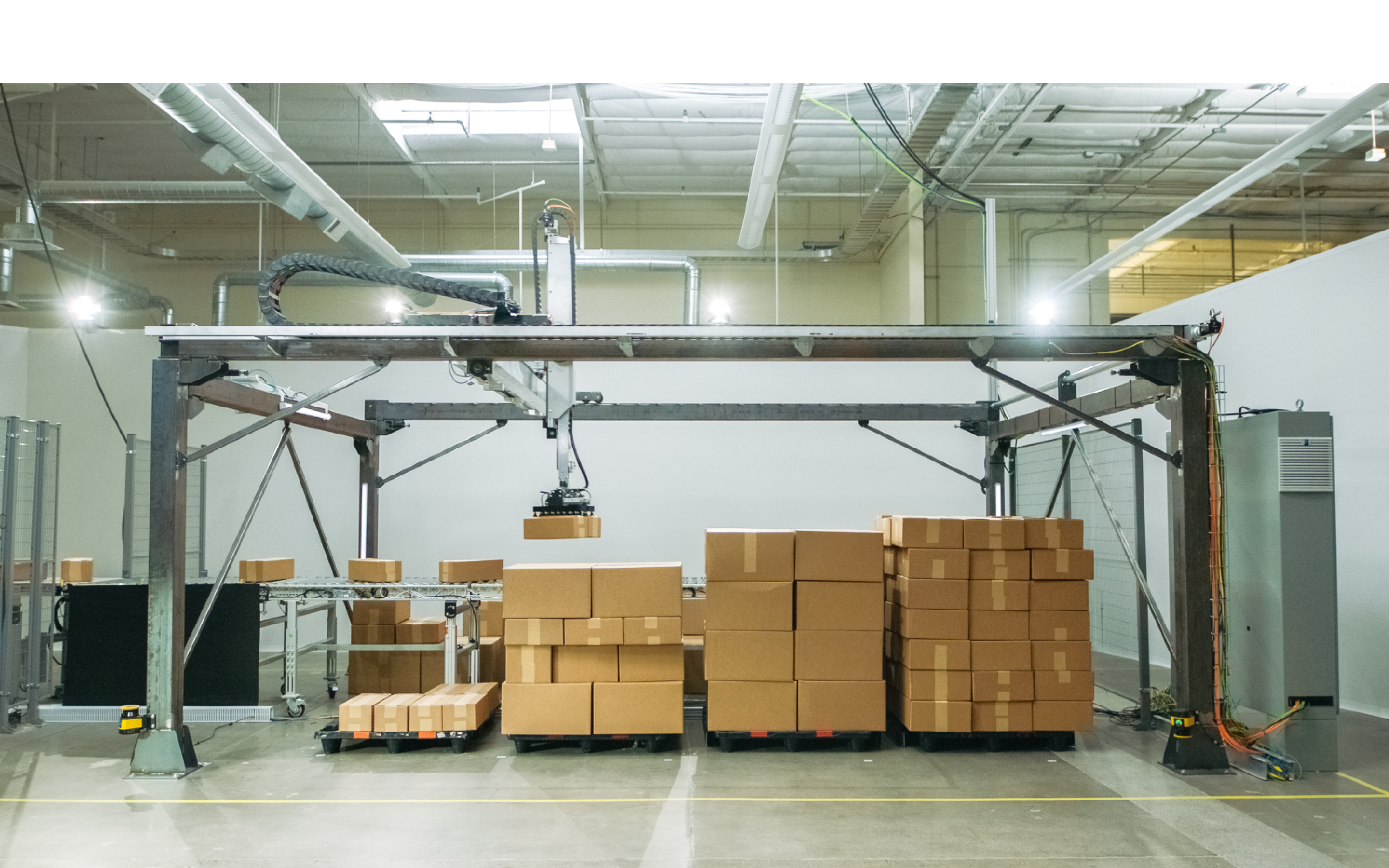
Automate Inbound
Automate Outbound
AmbiStack is configurable by design

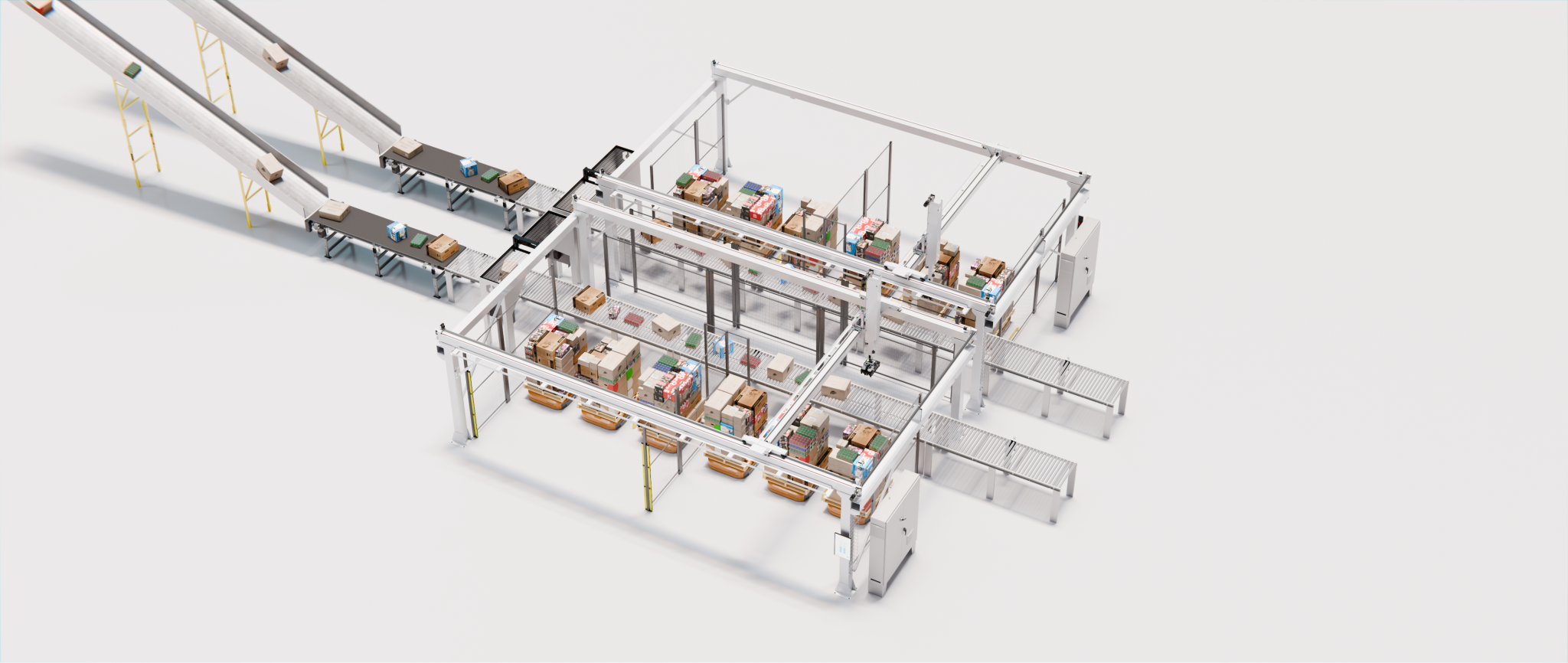
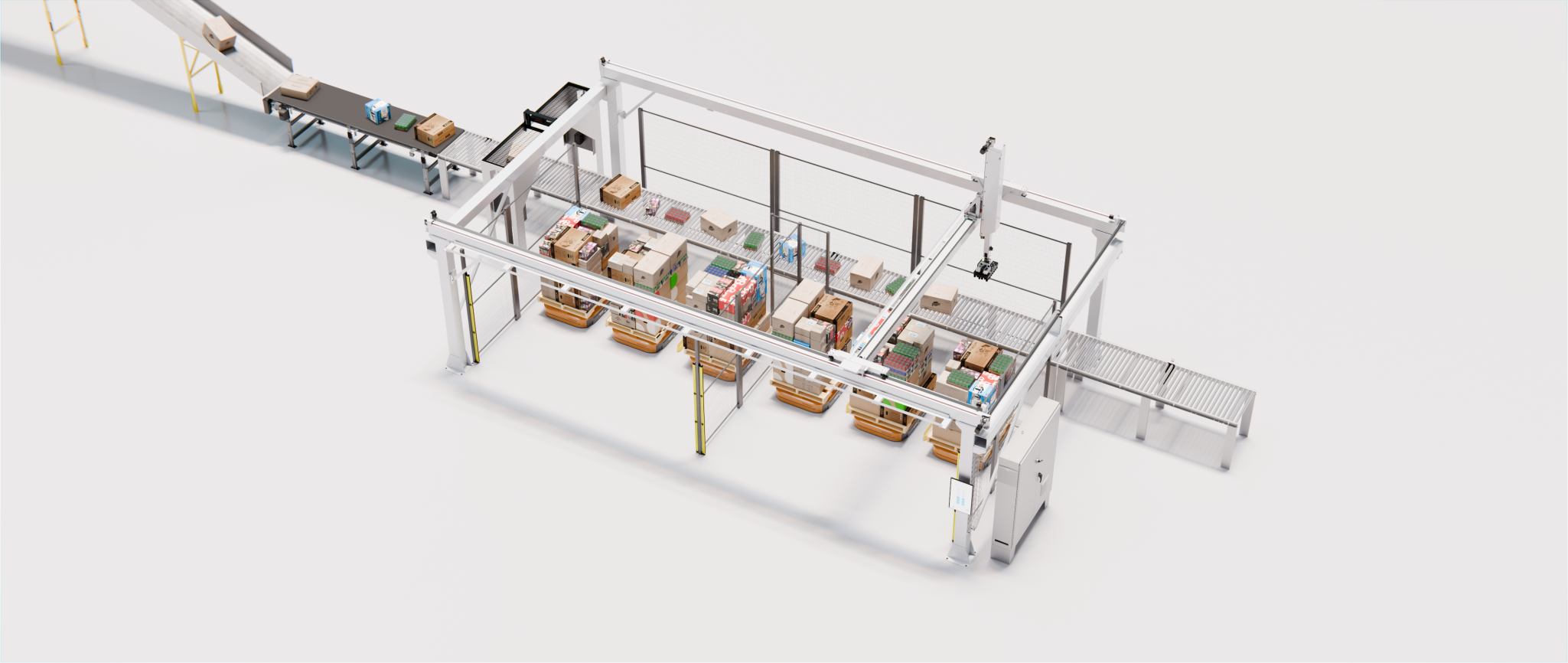
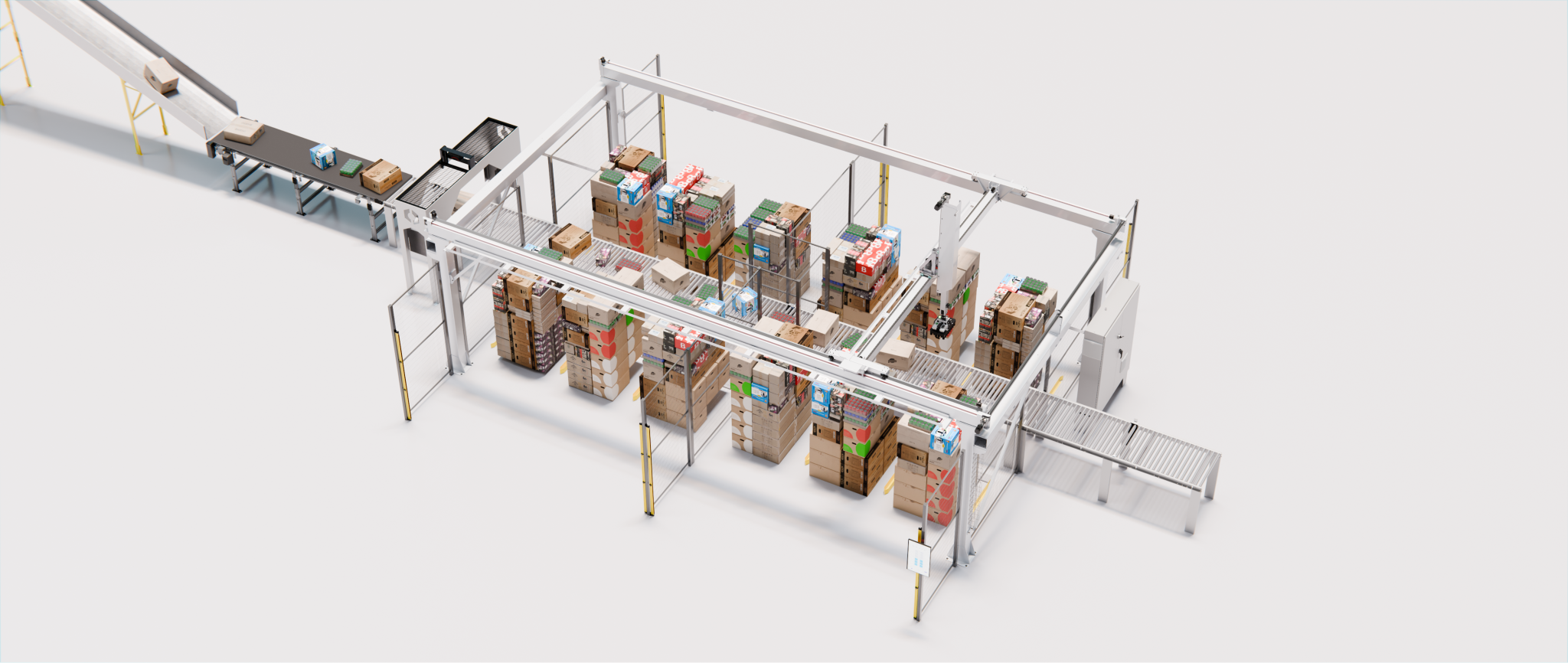
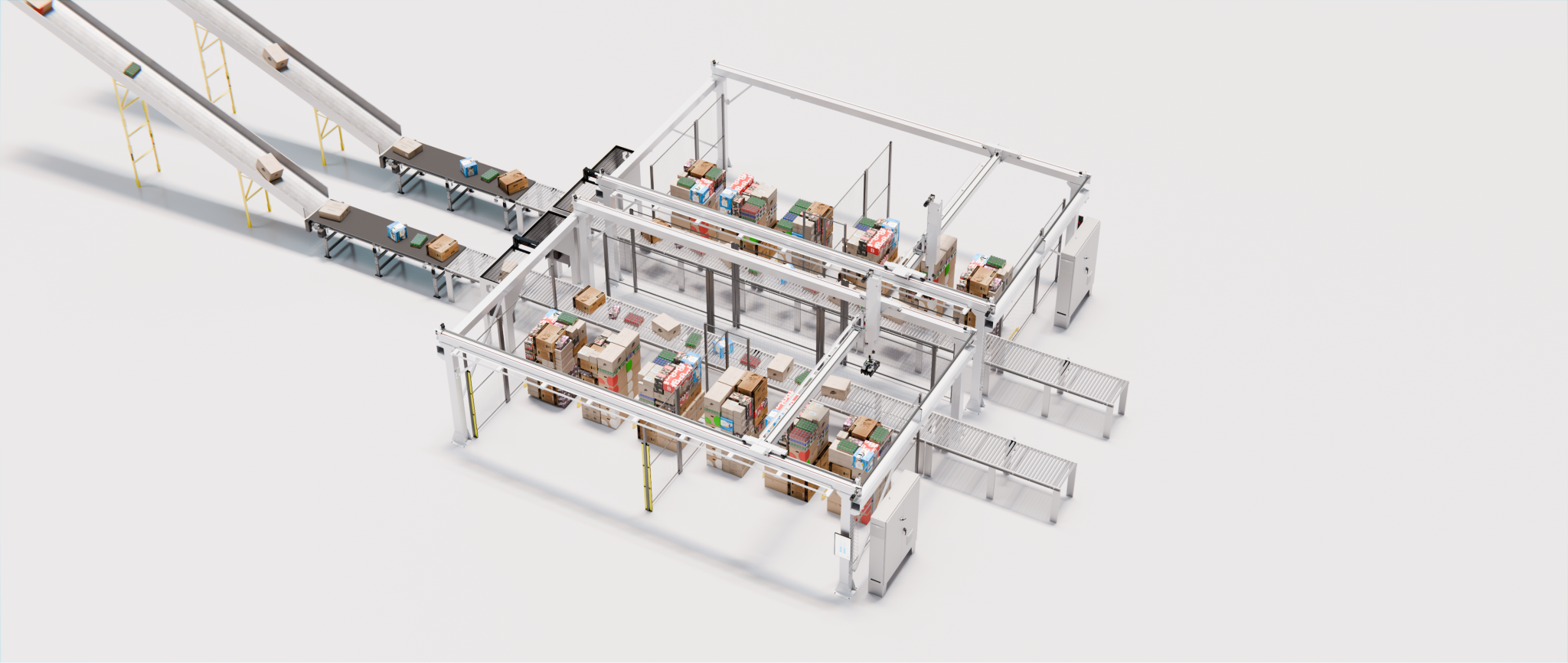
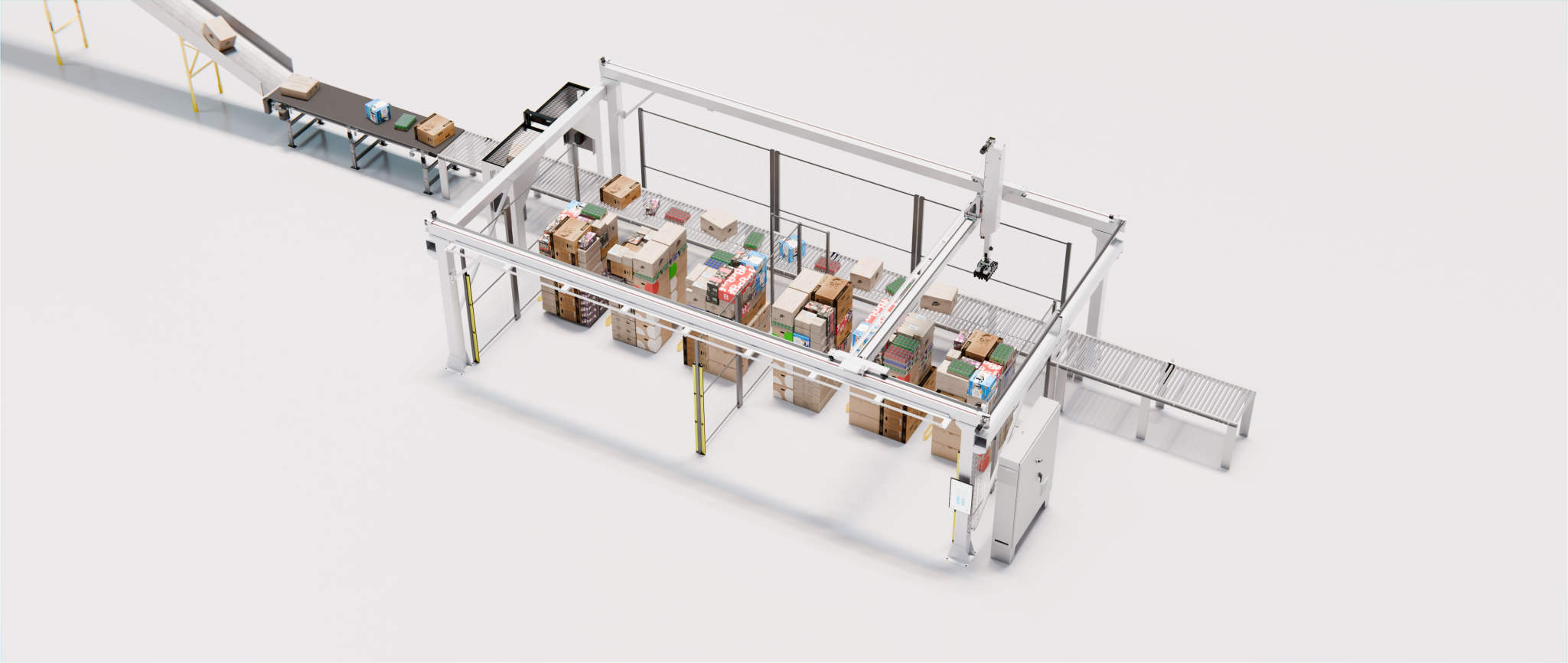
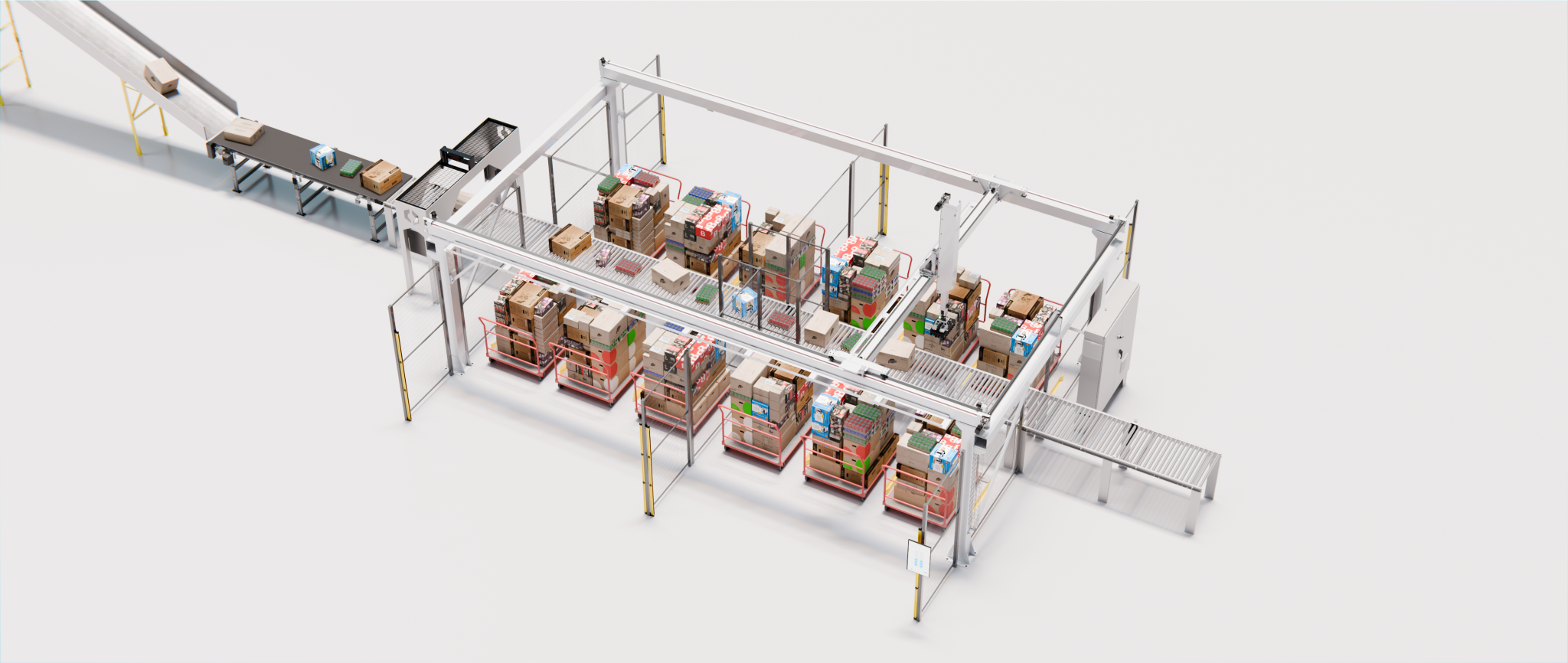
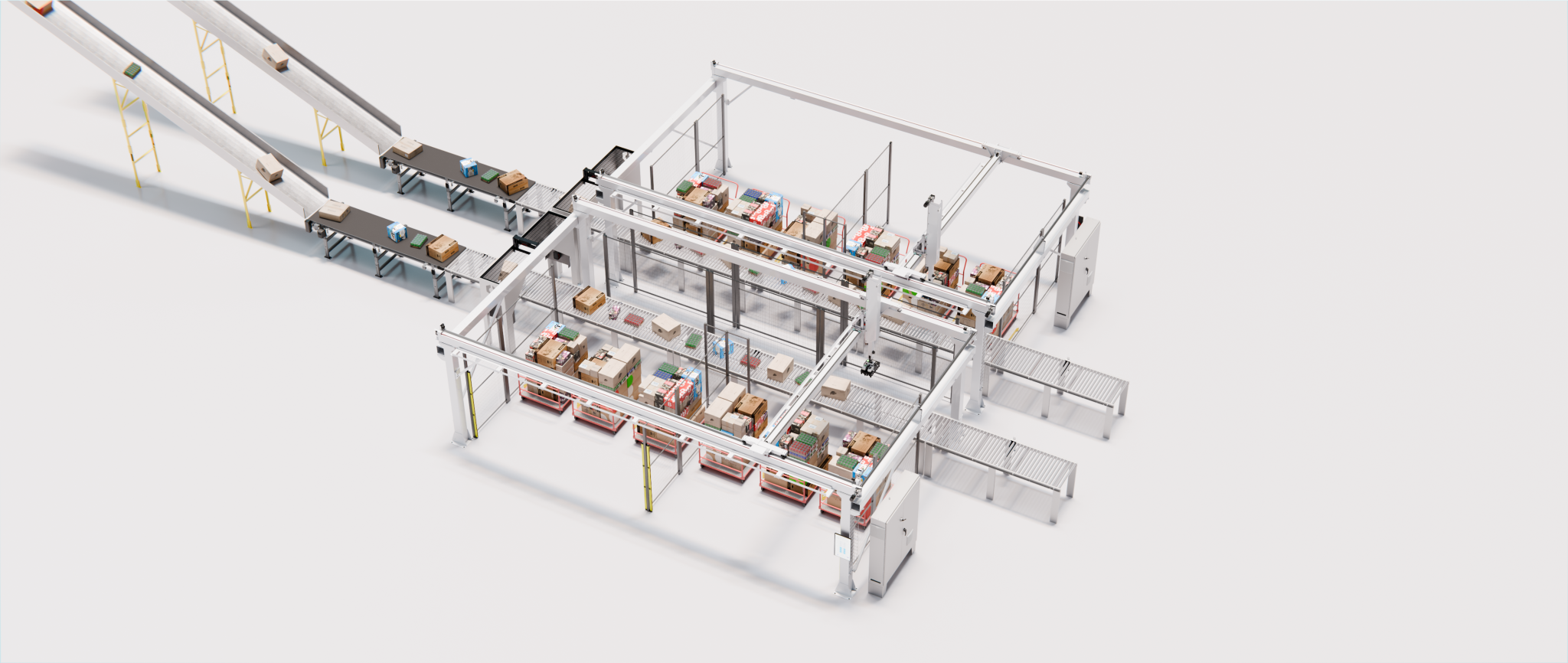
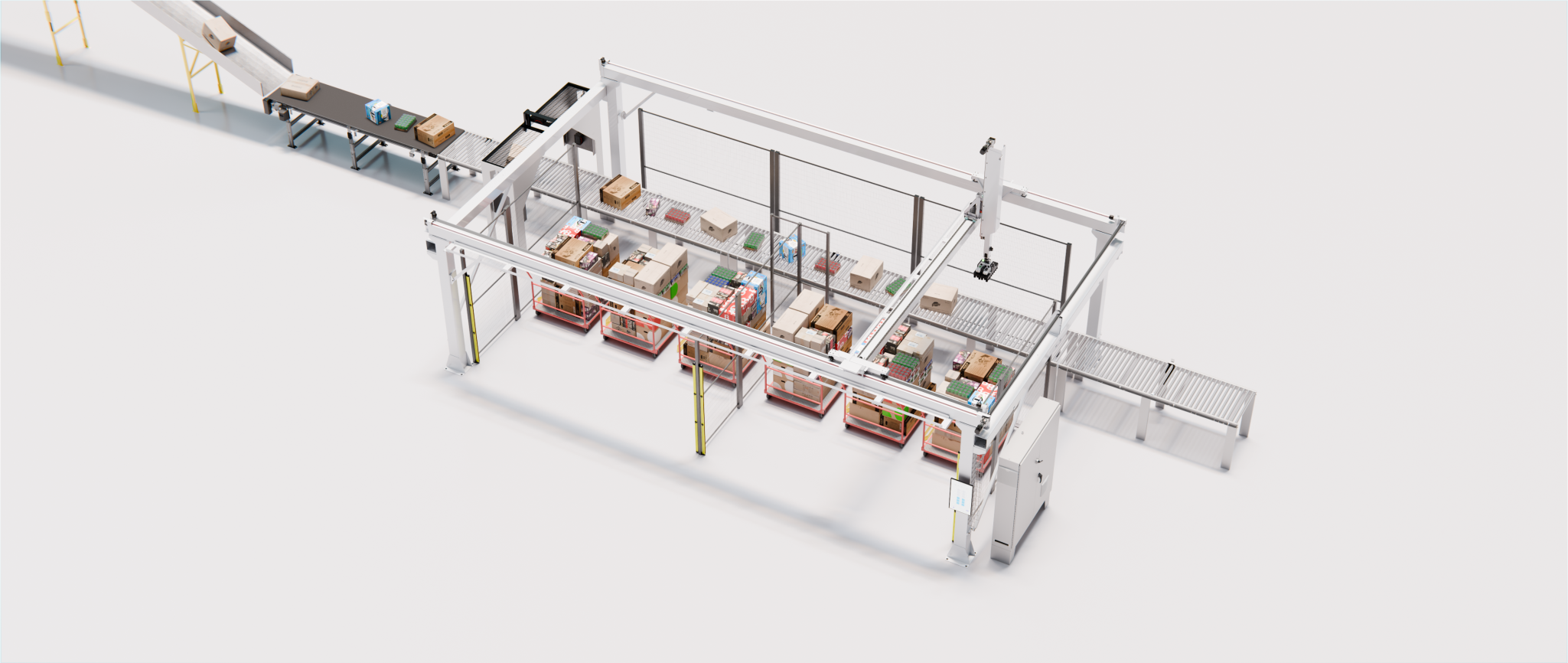
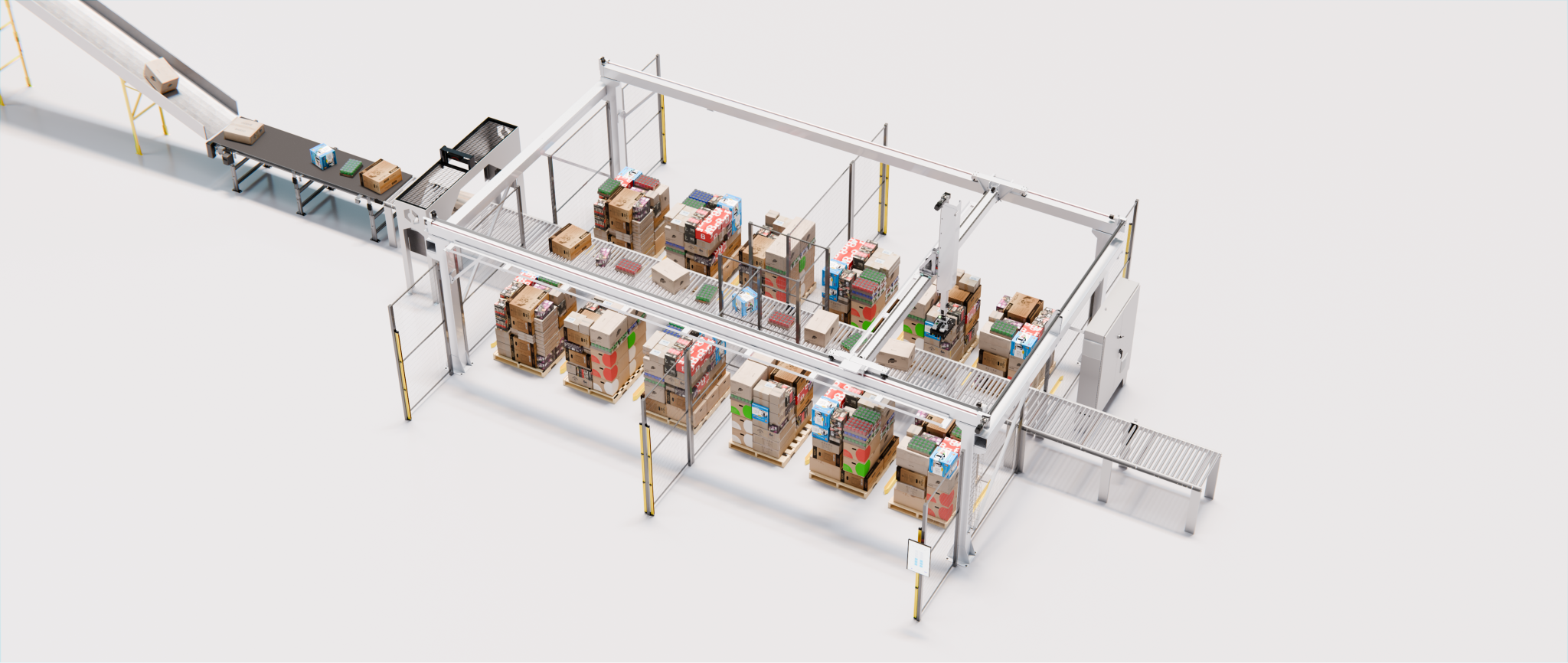
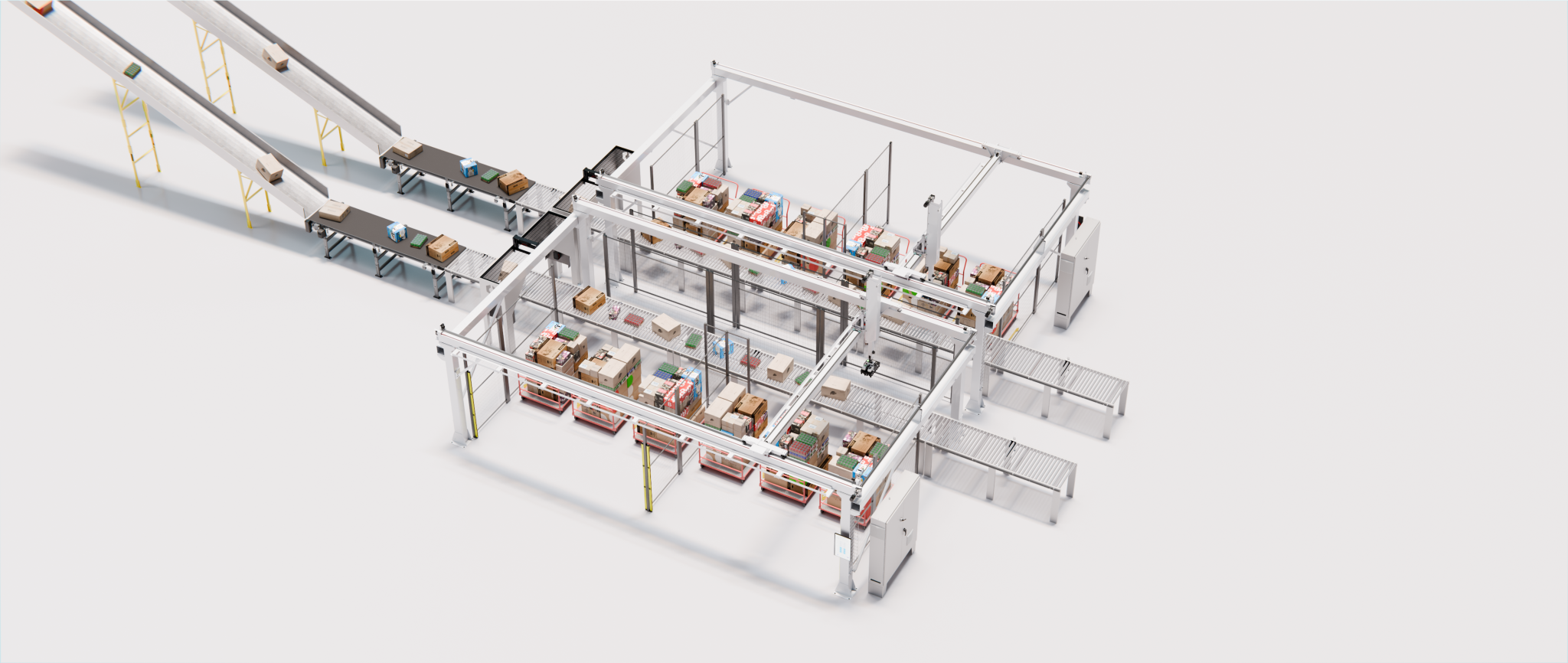
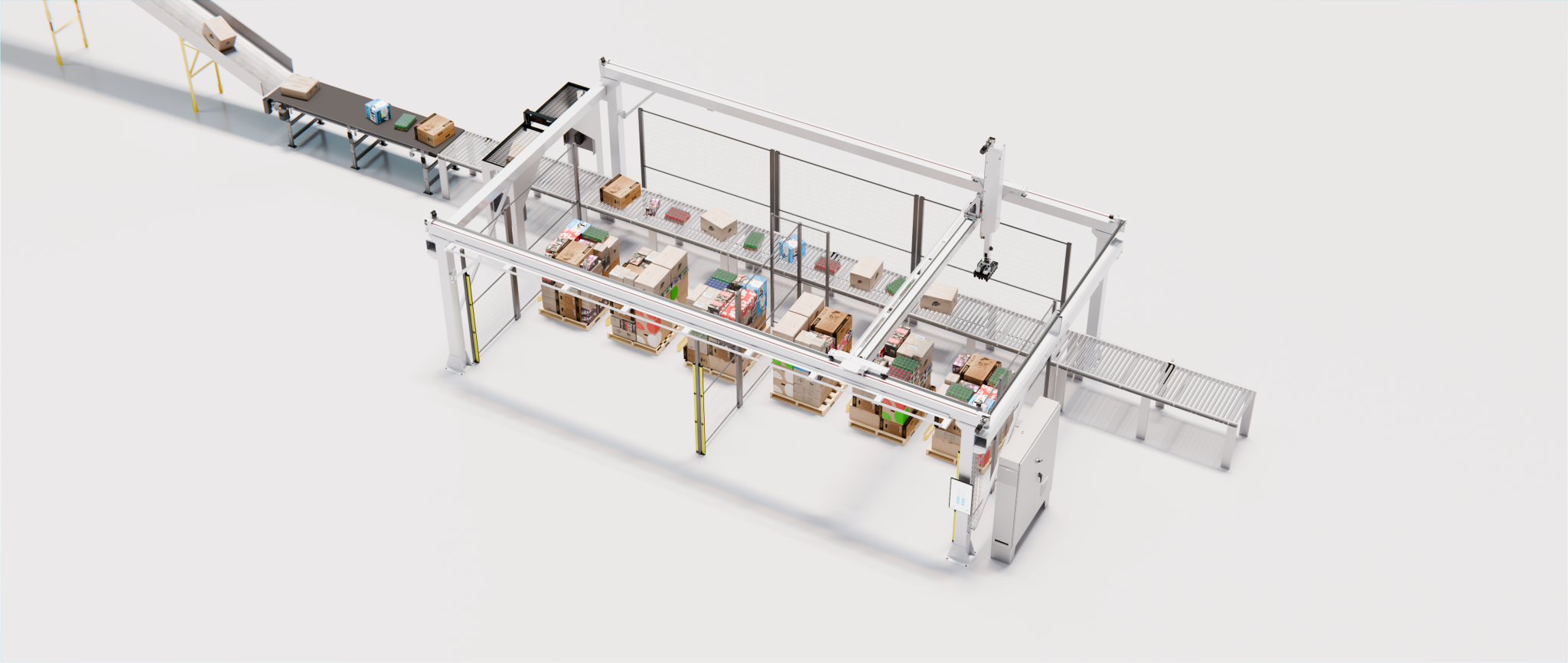
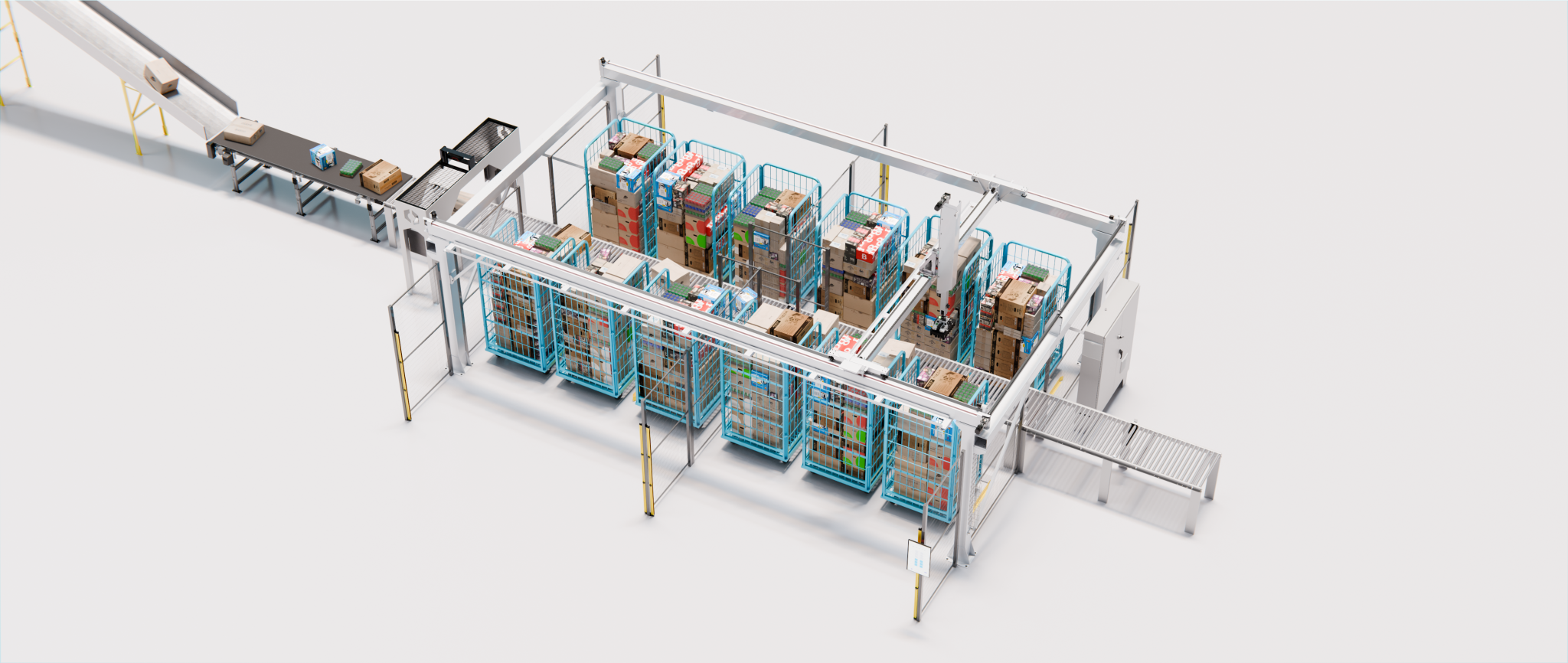
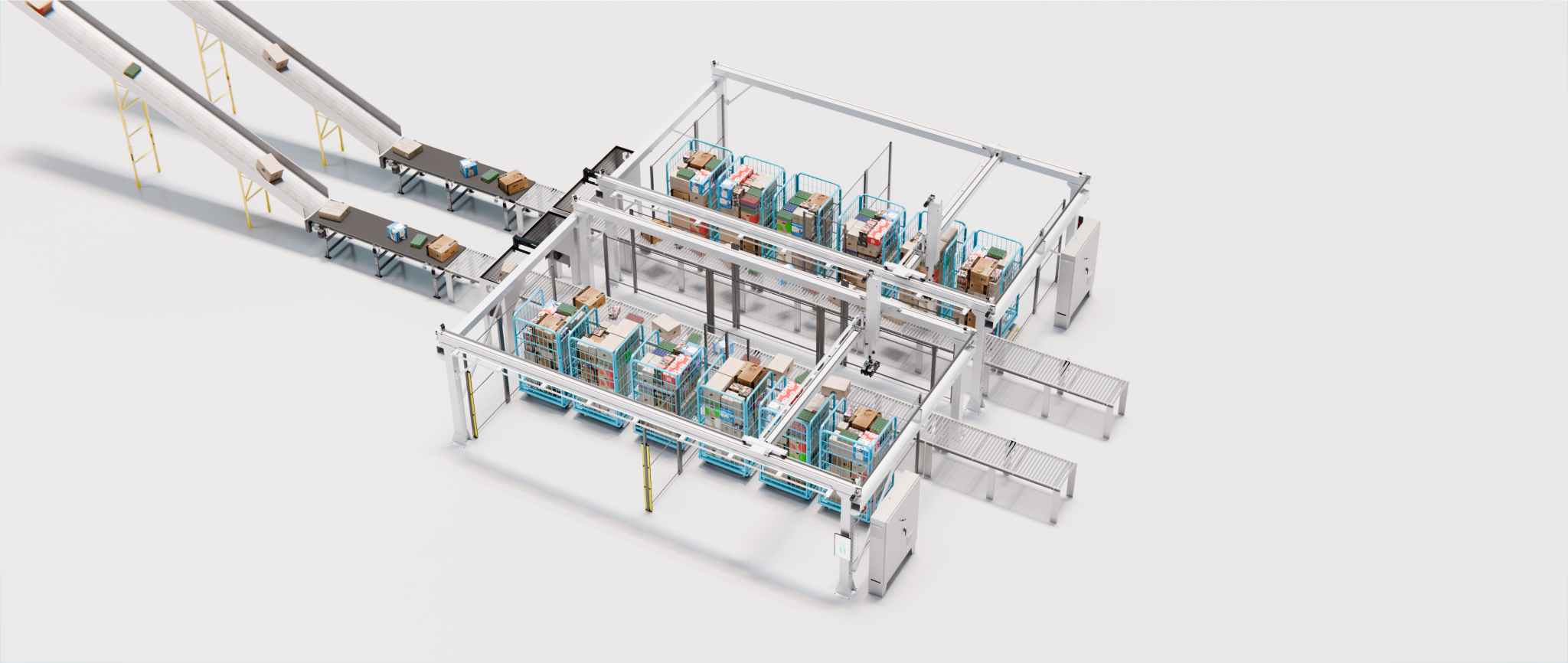
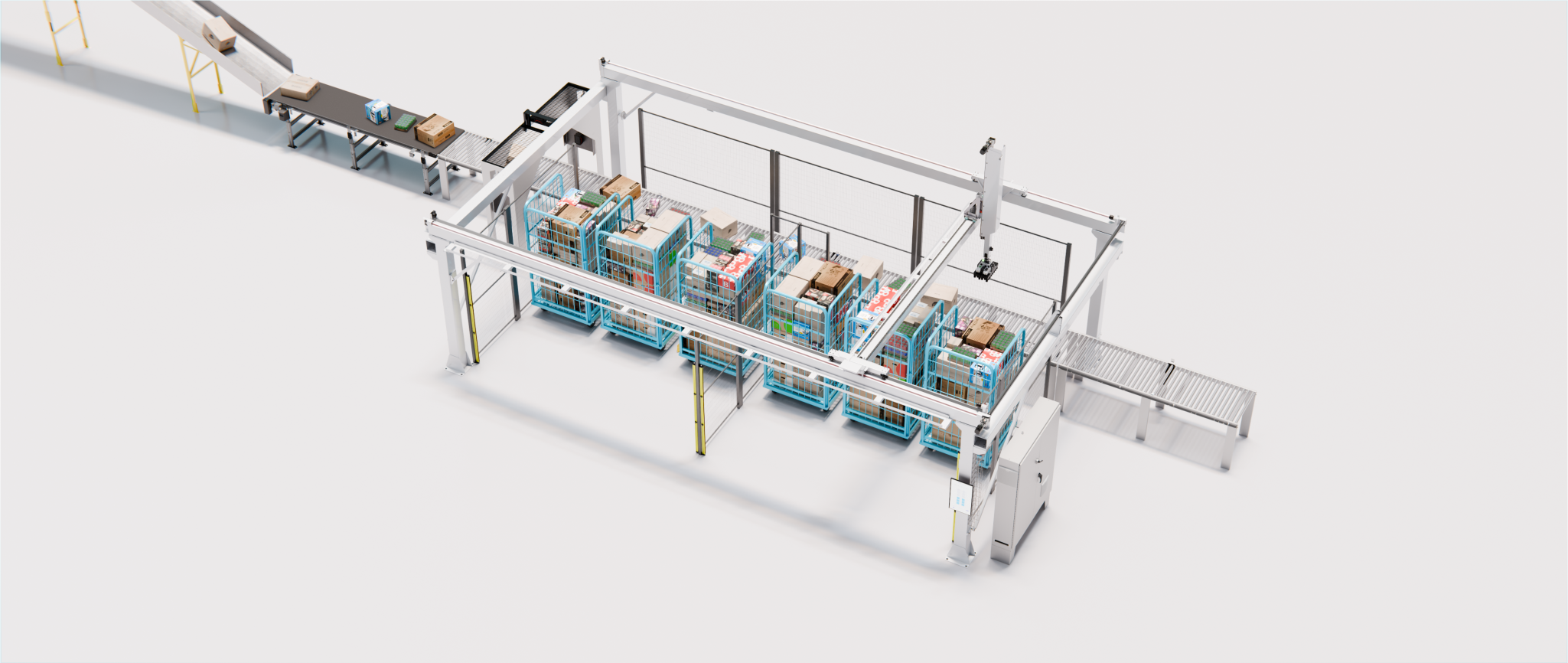
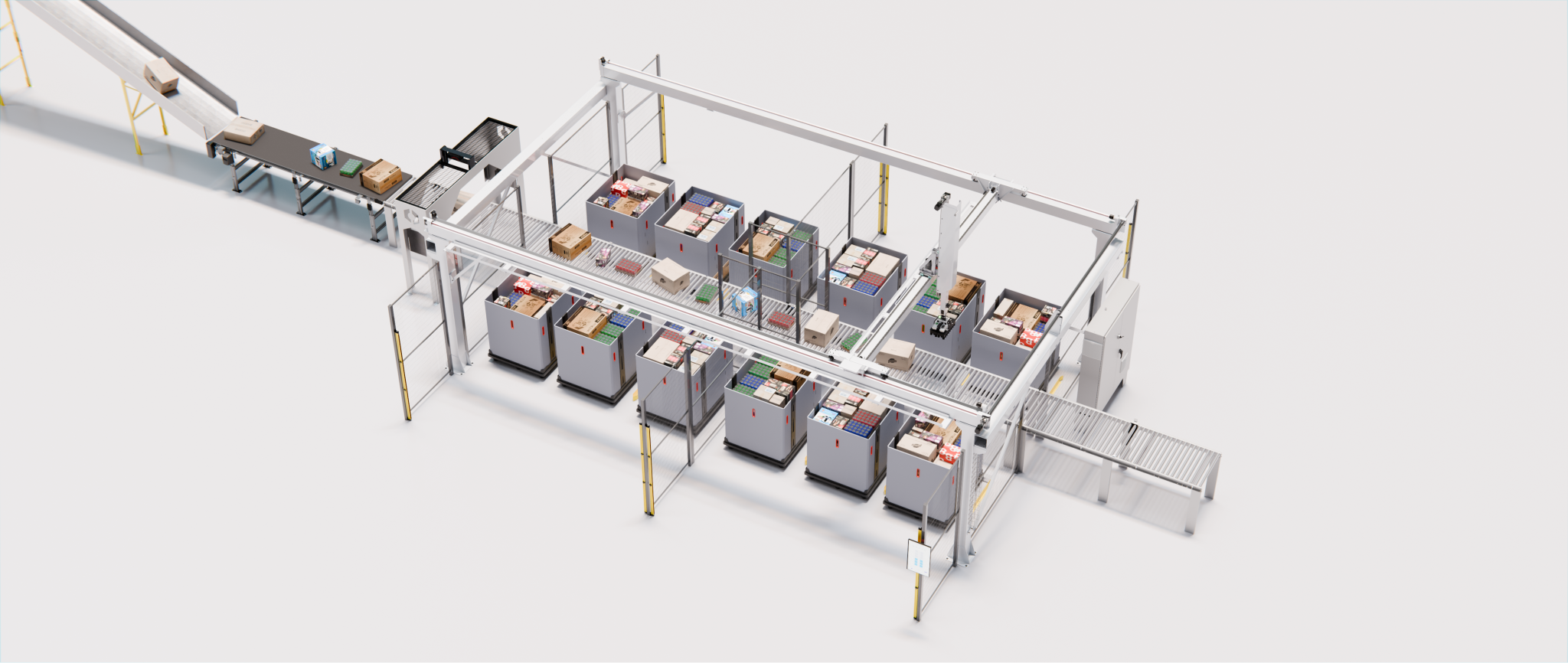
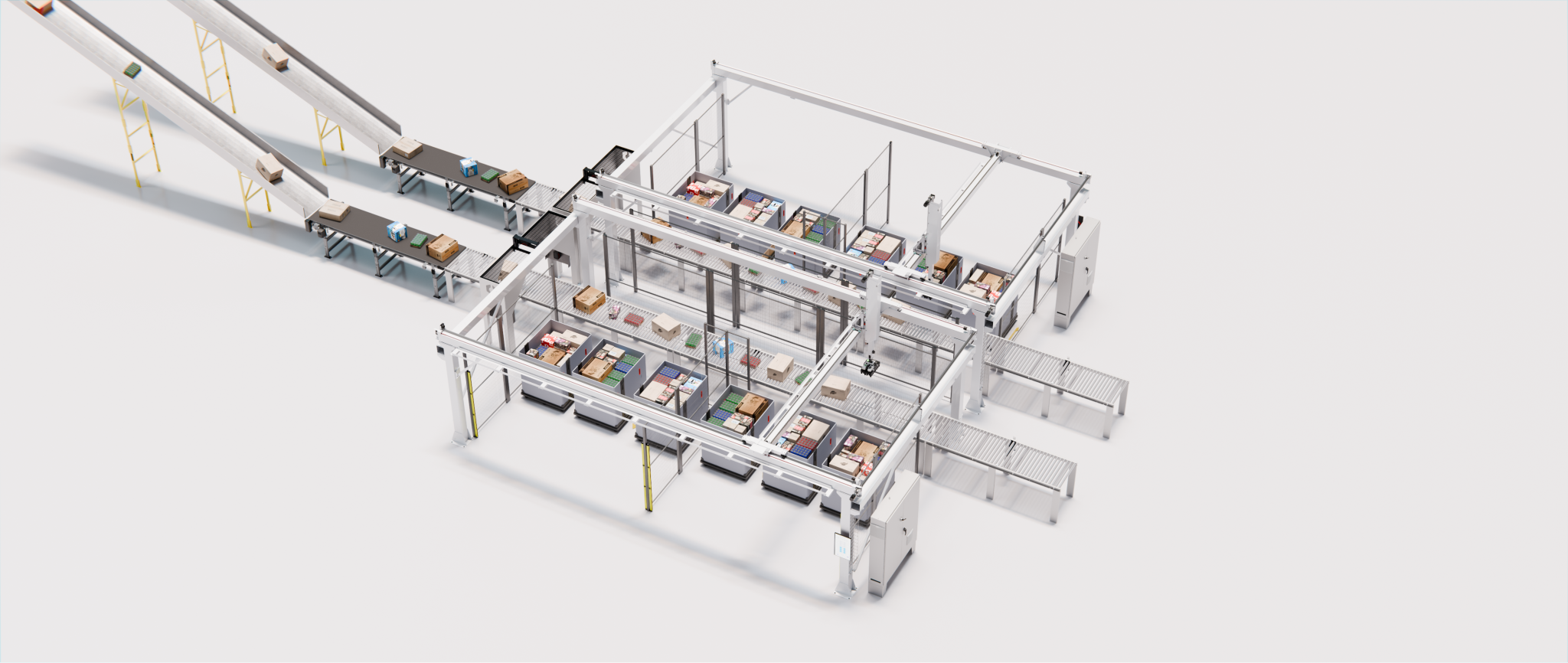
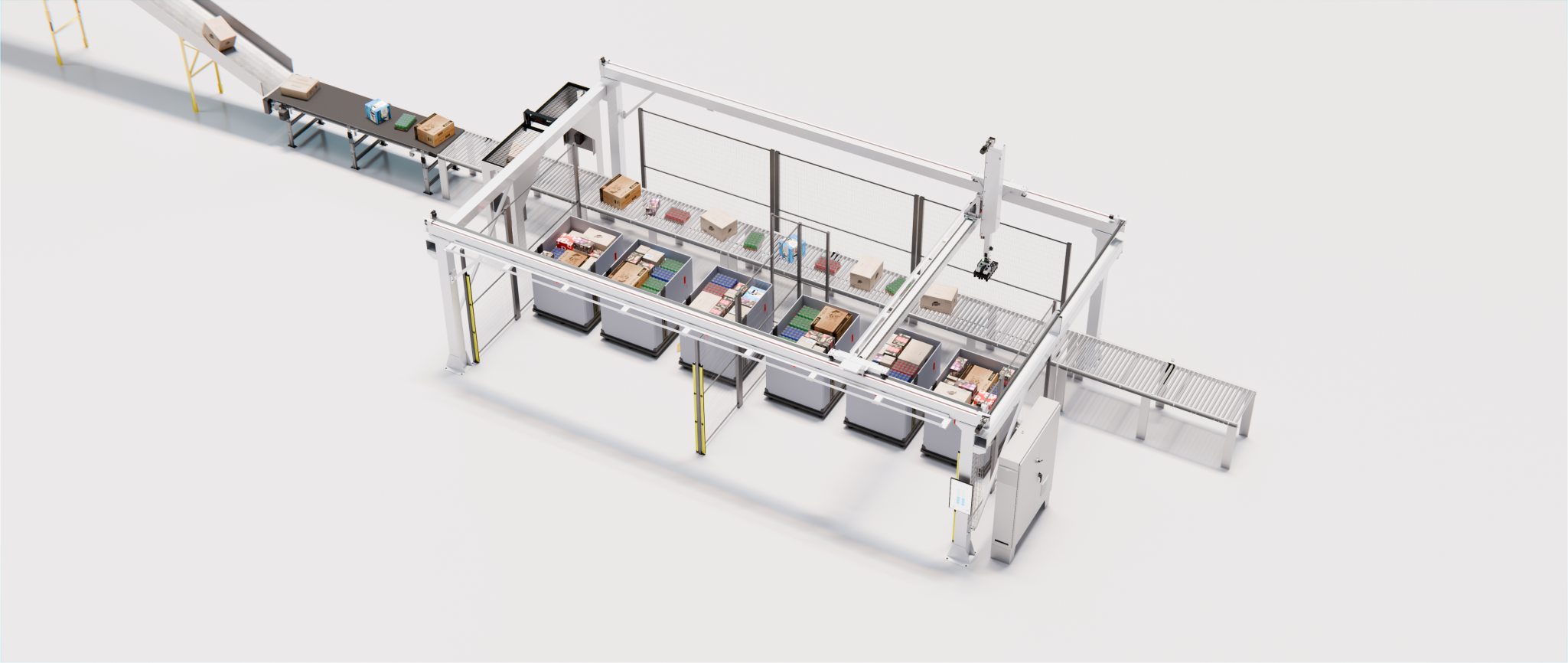
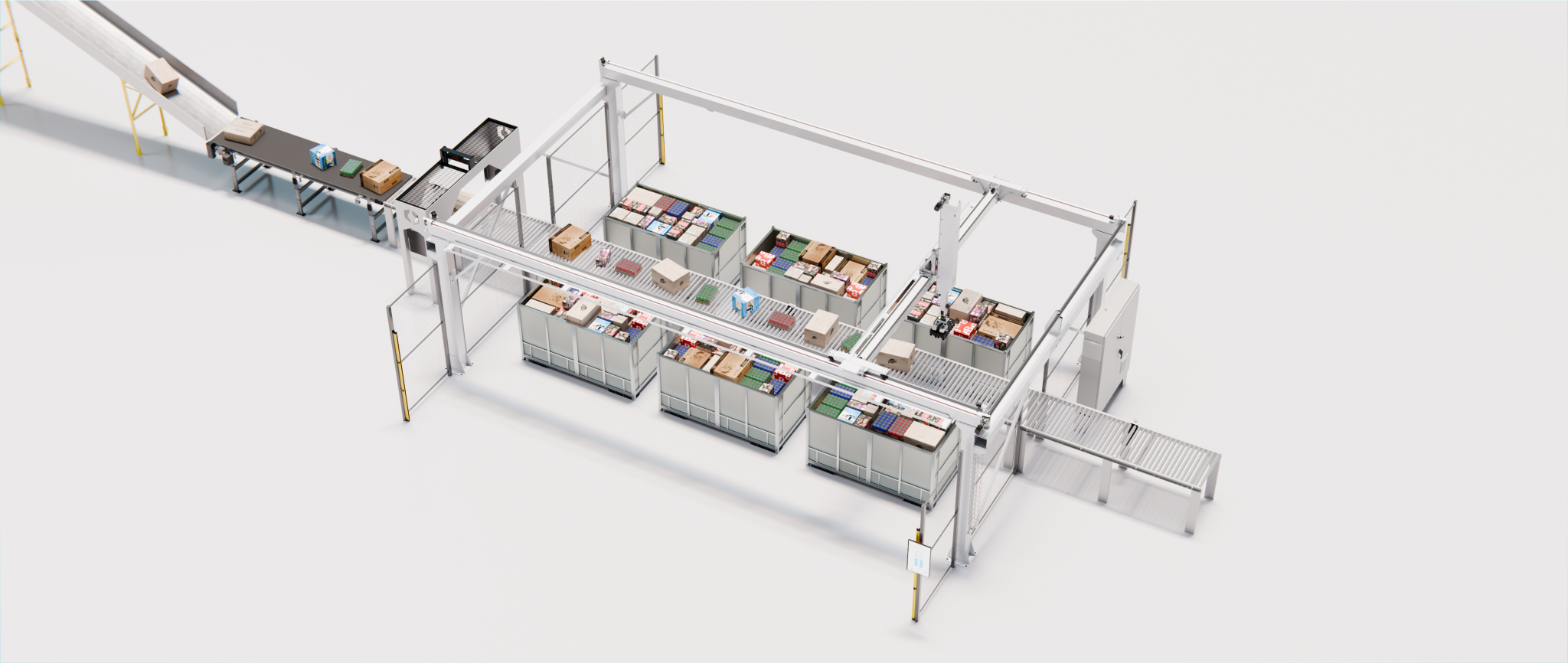
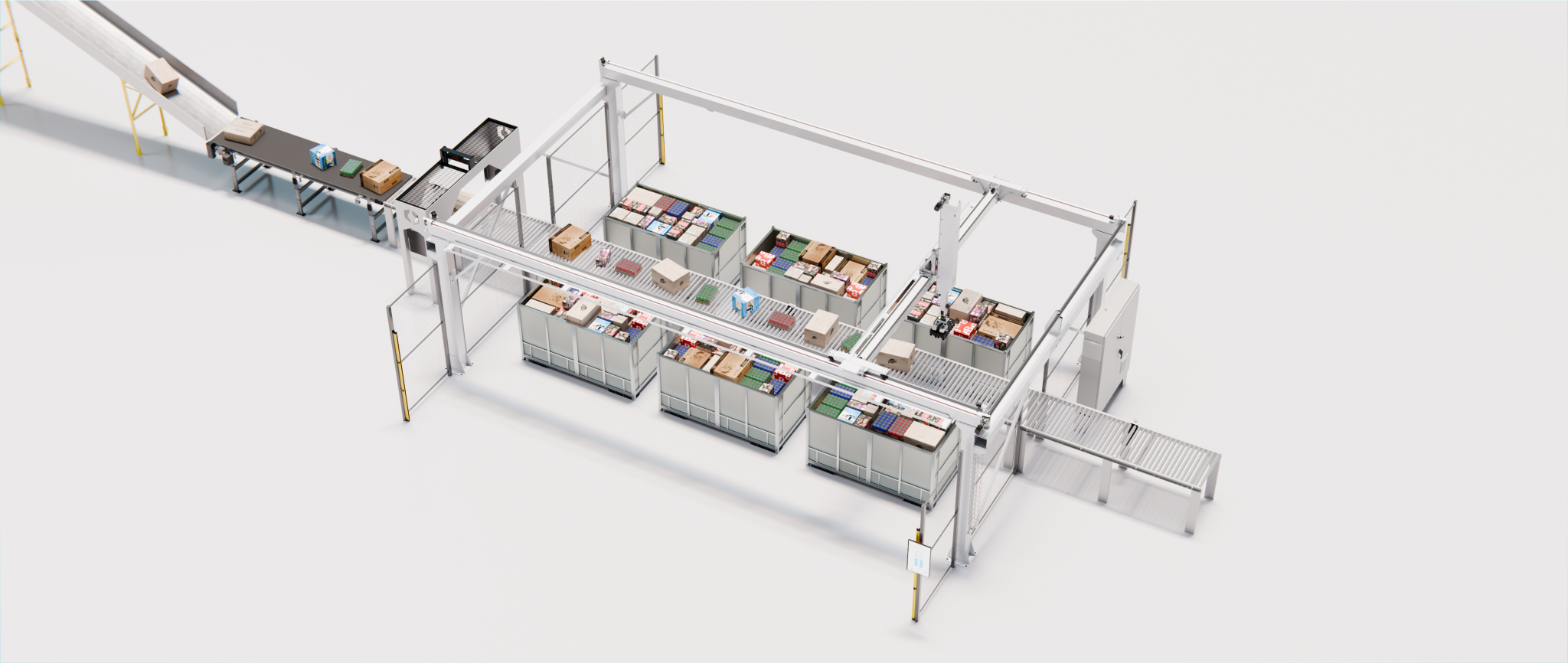
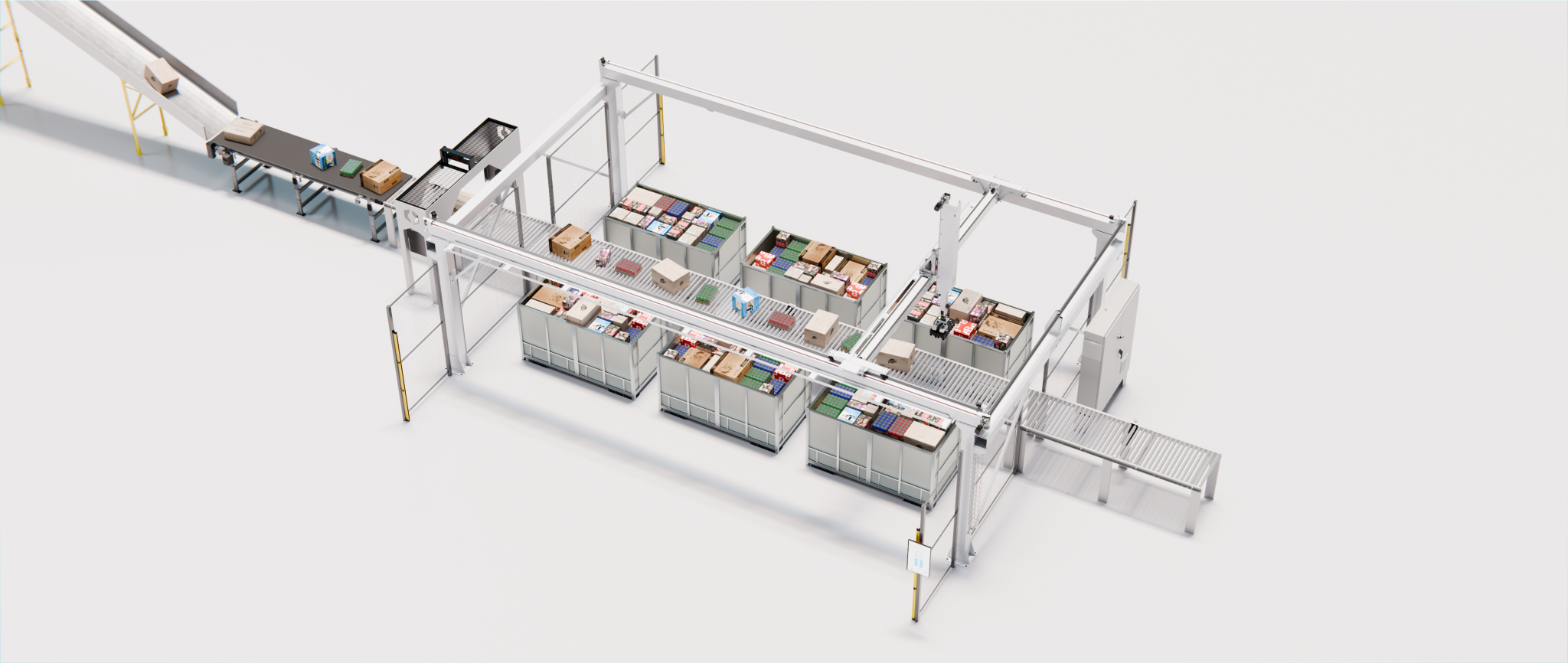
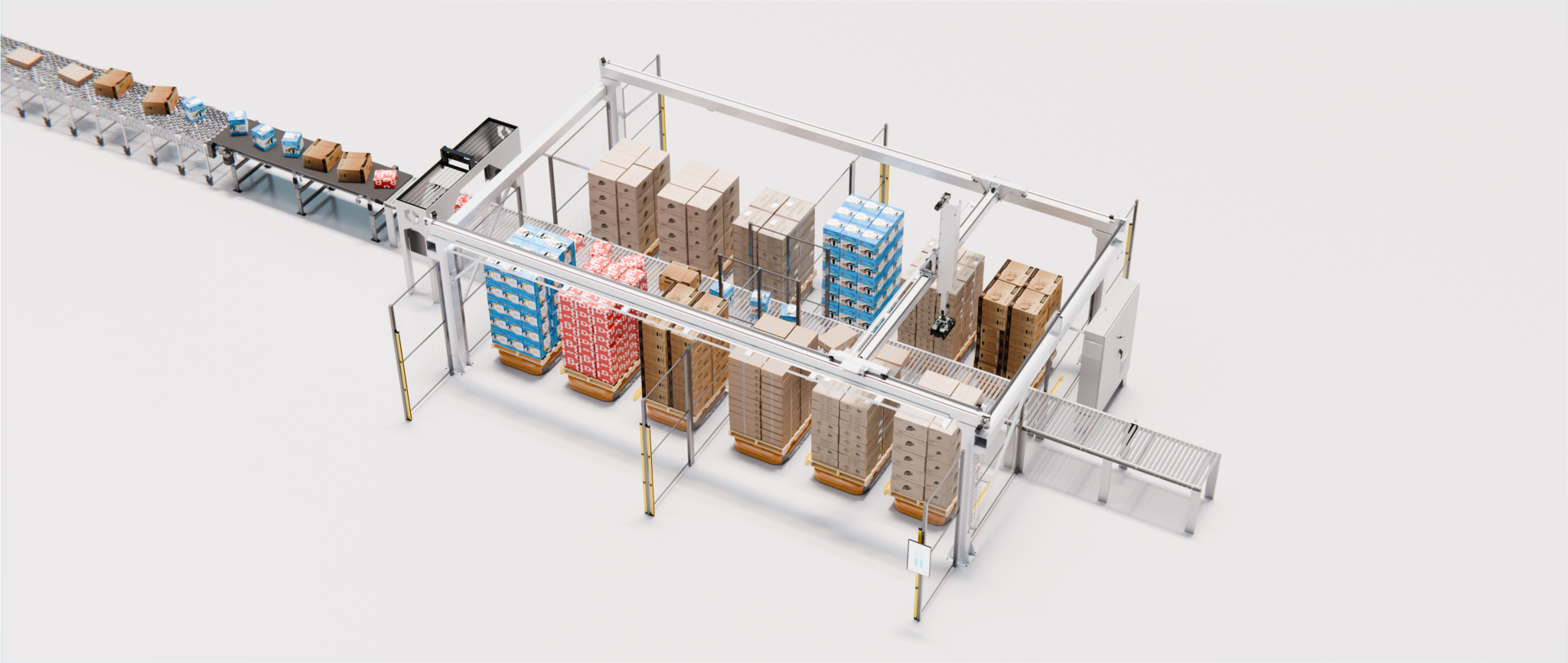
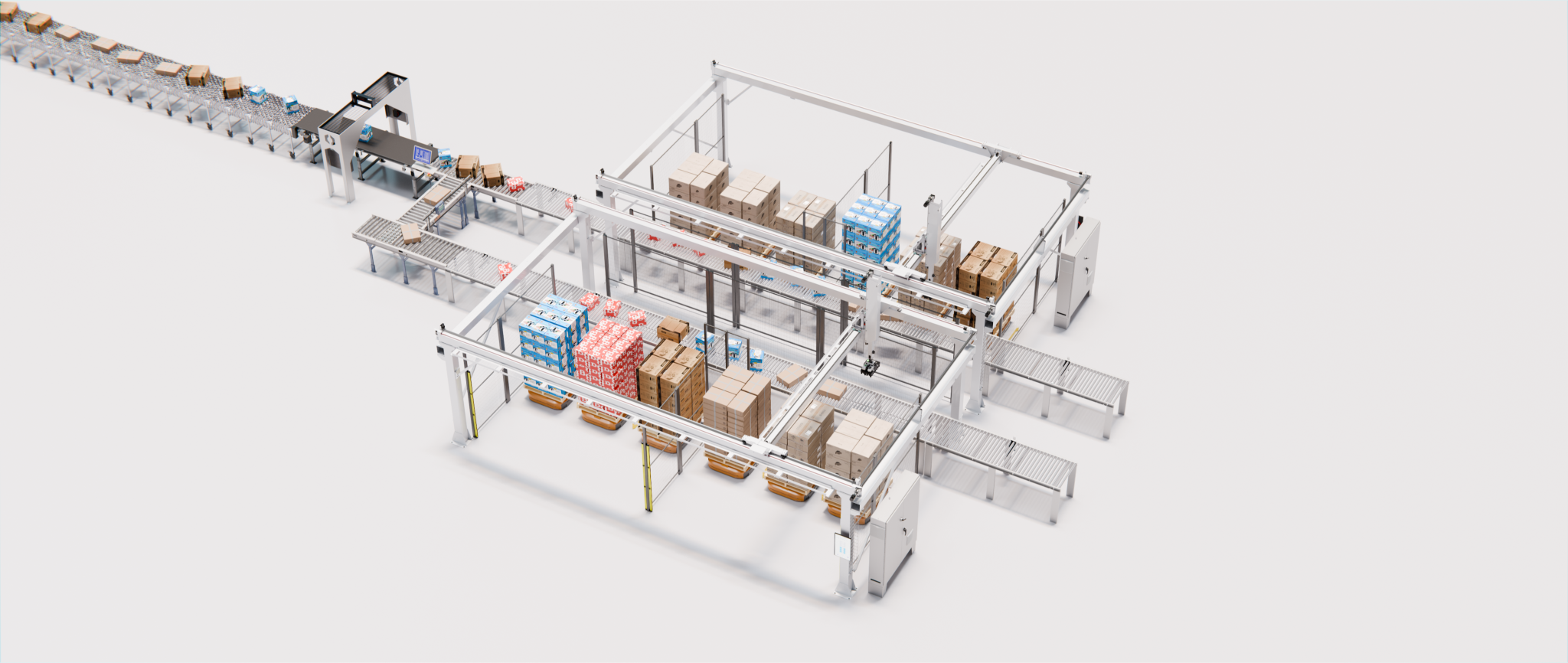
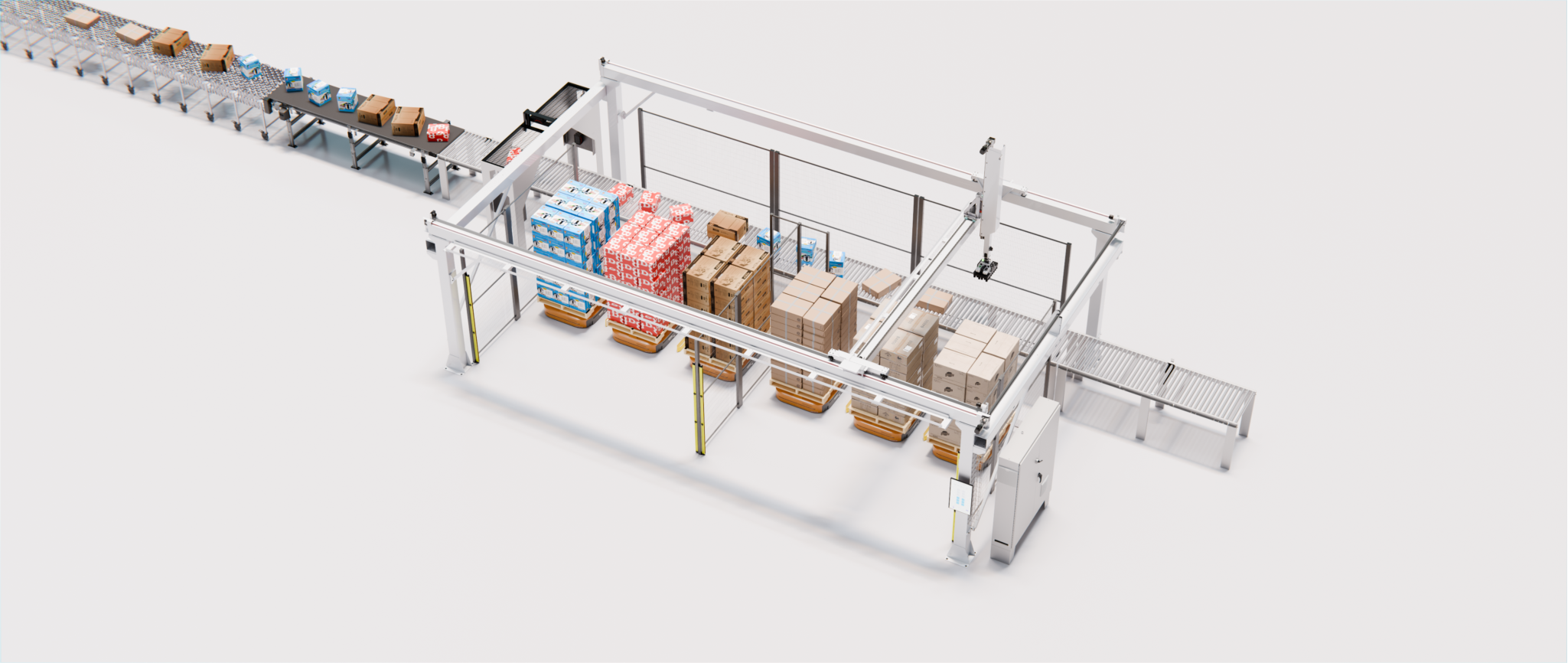
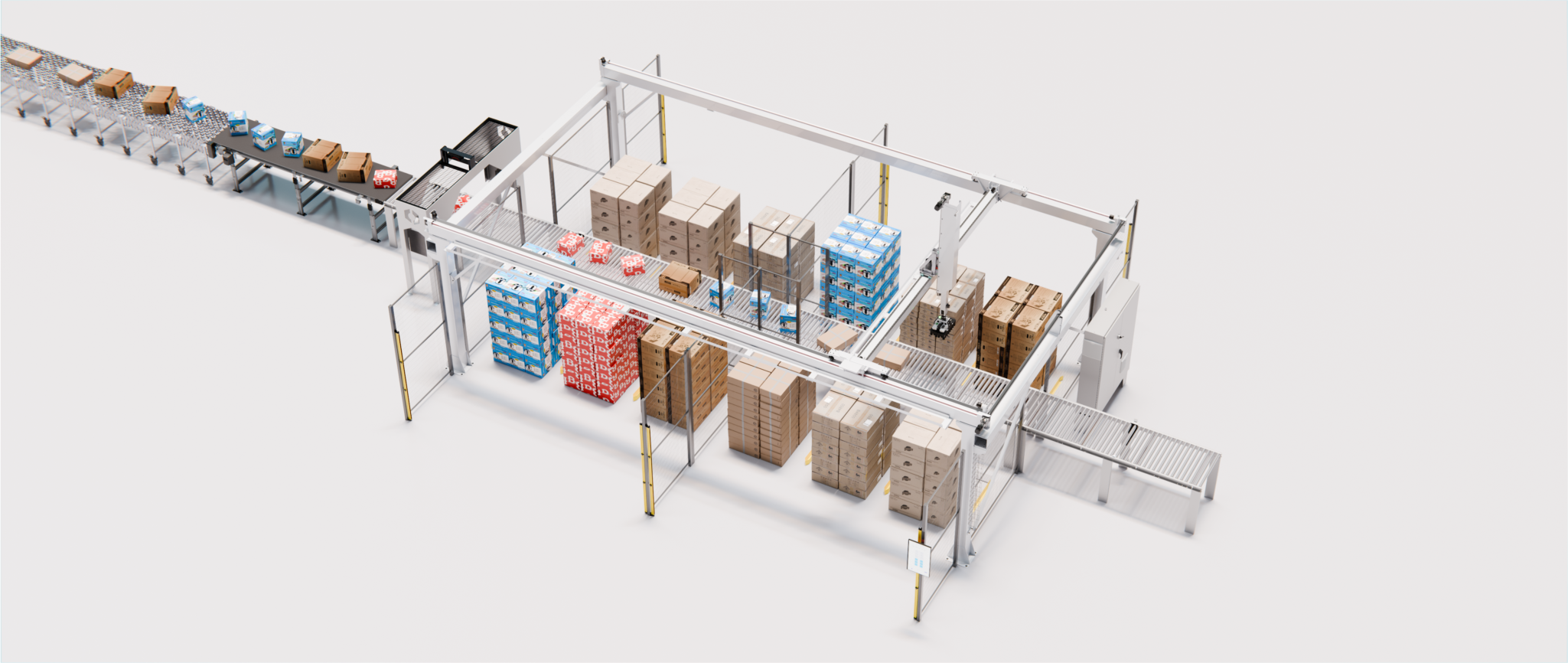
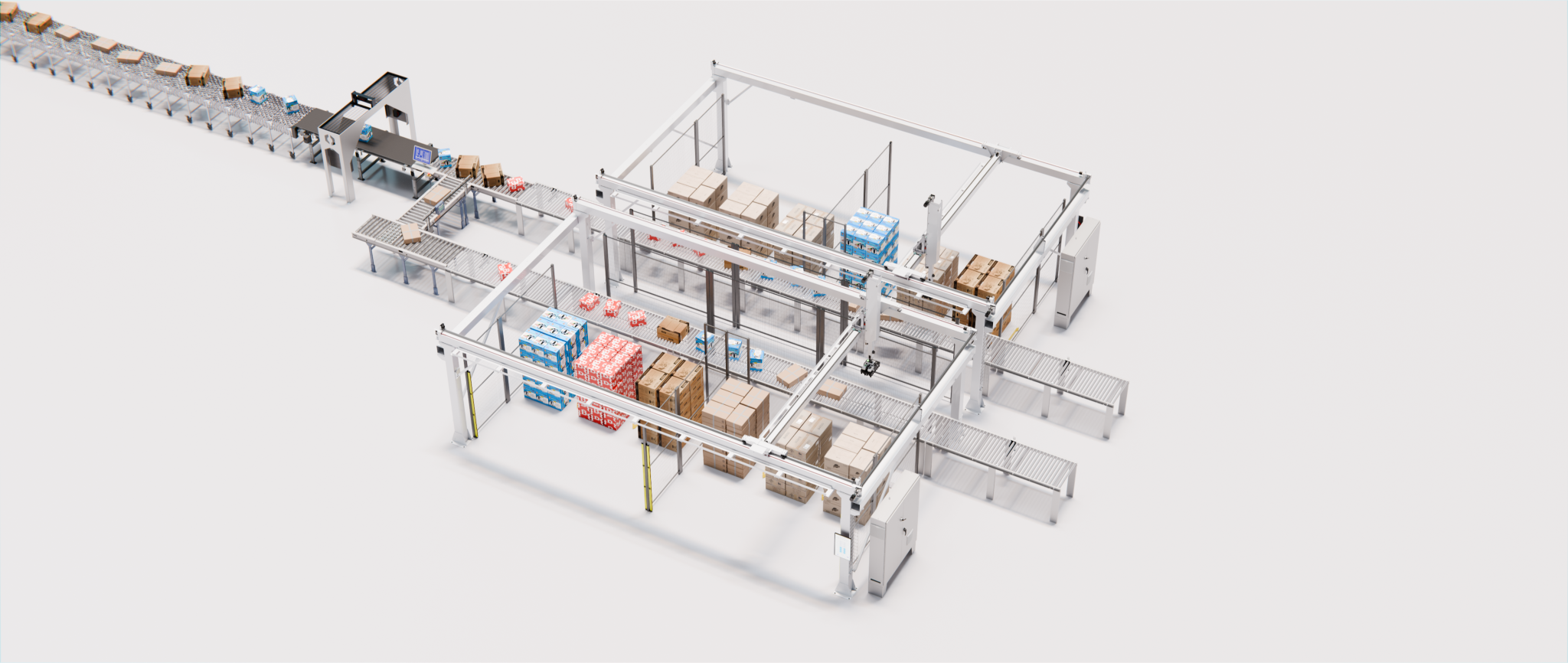
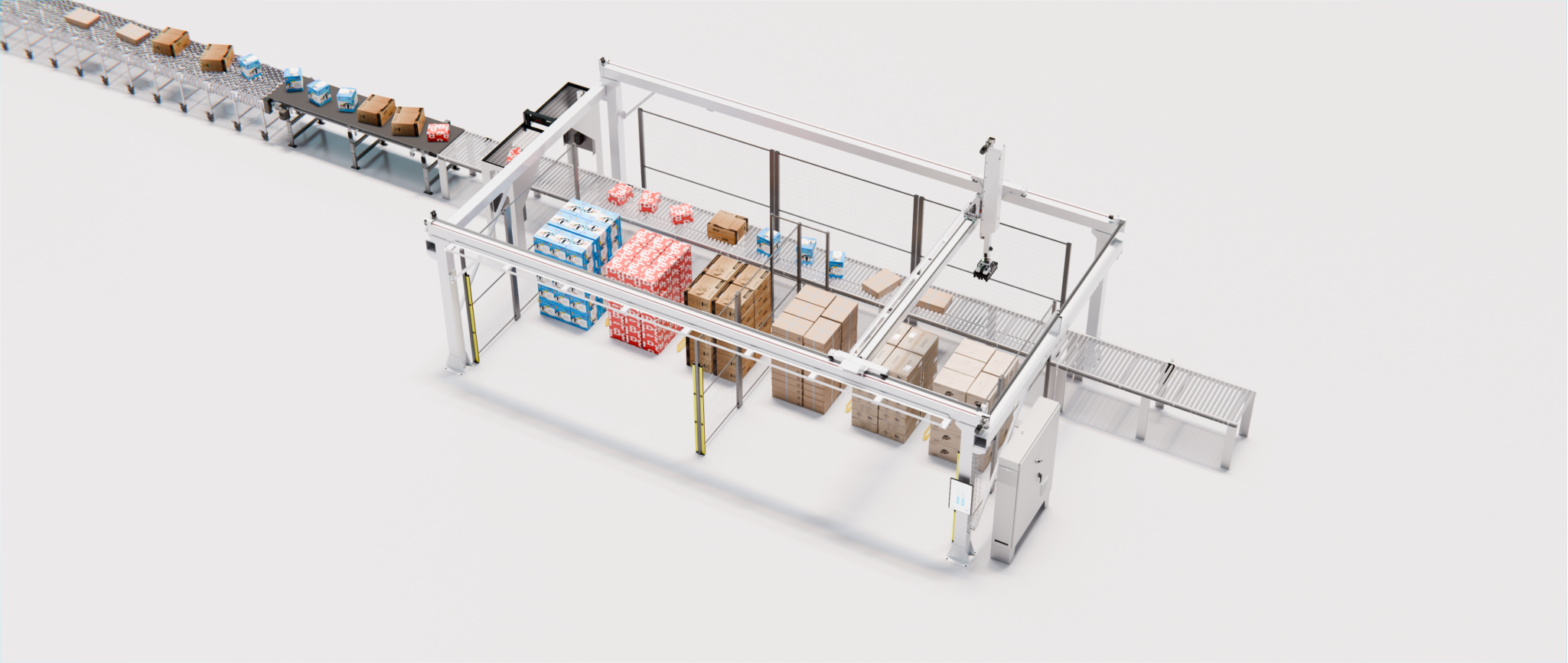
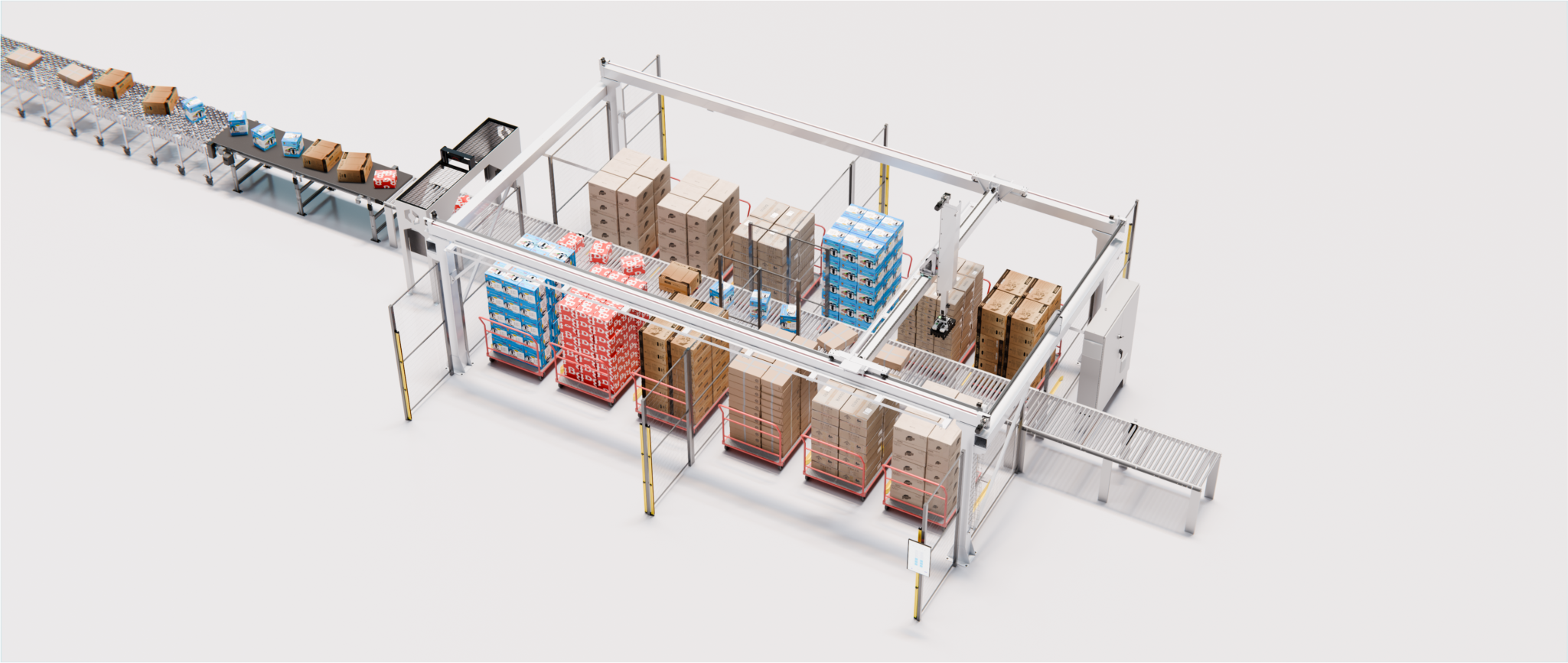
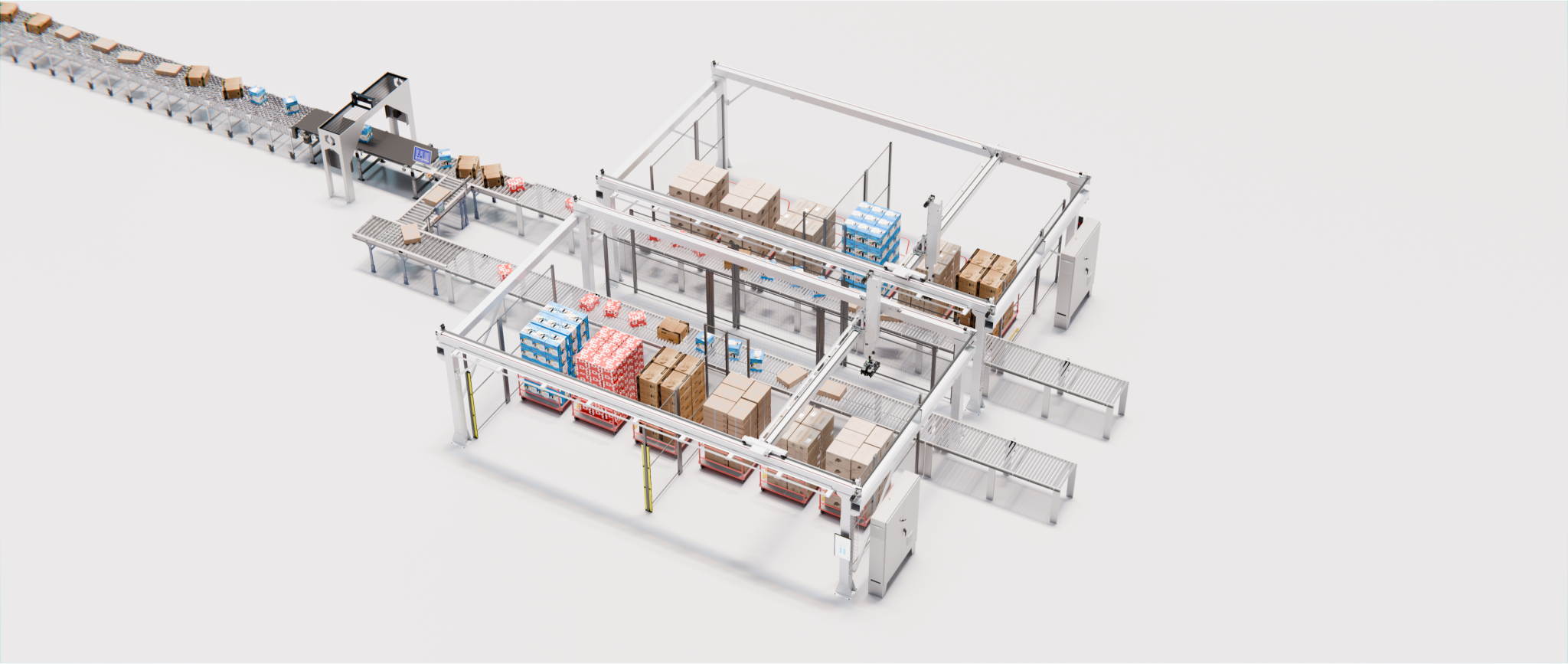
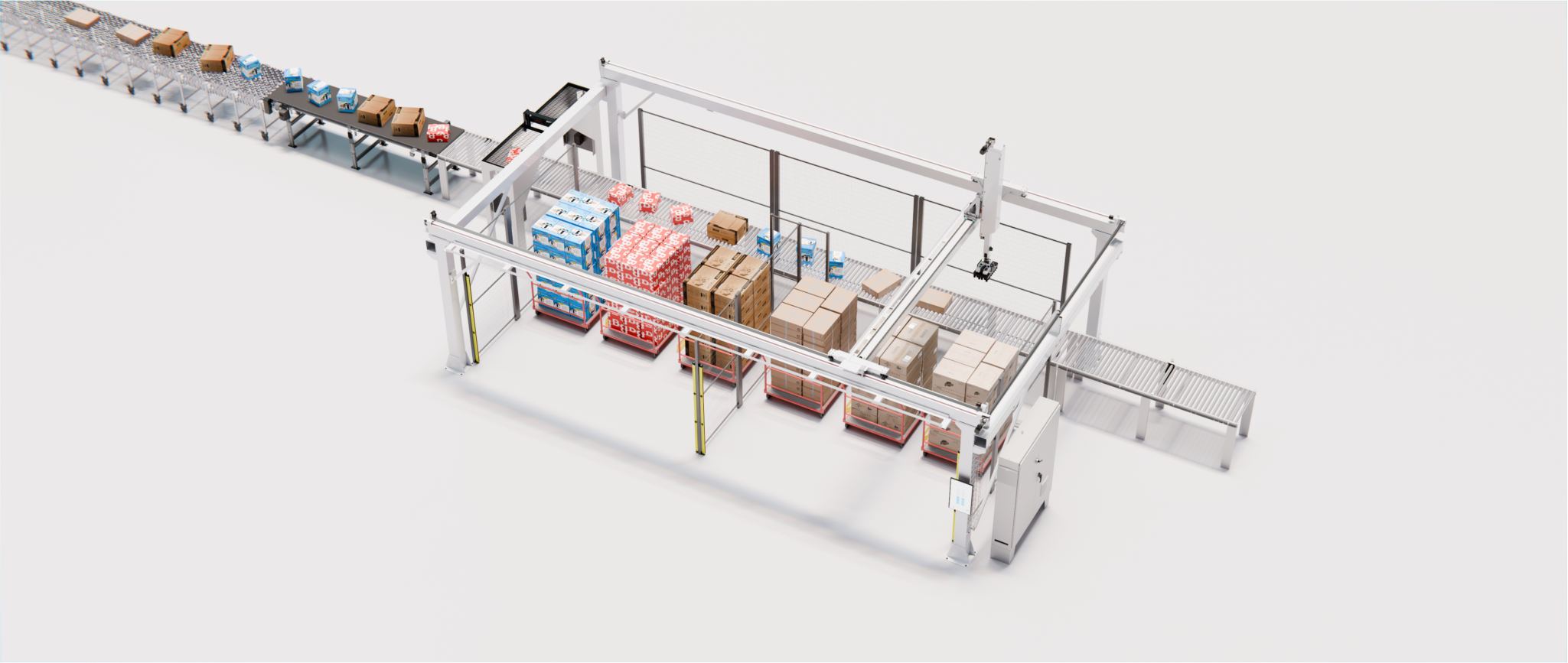
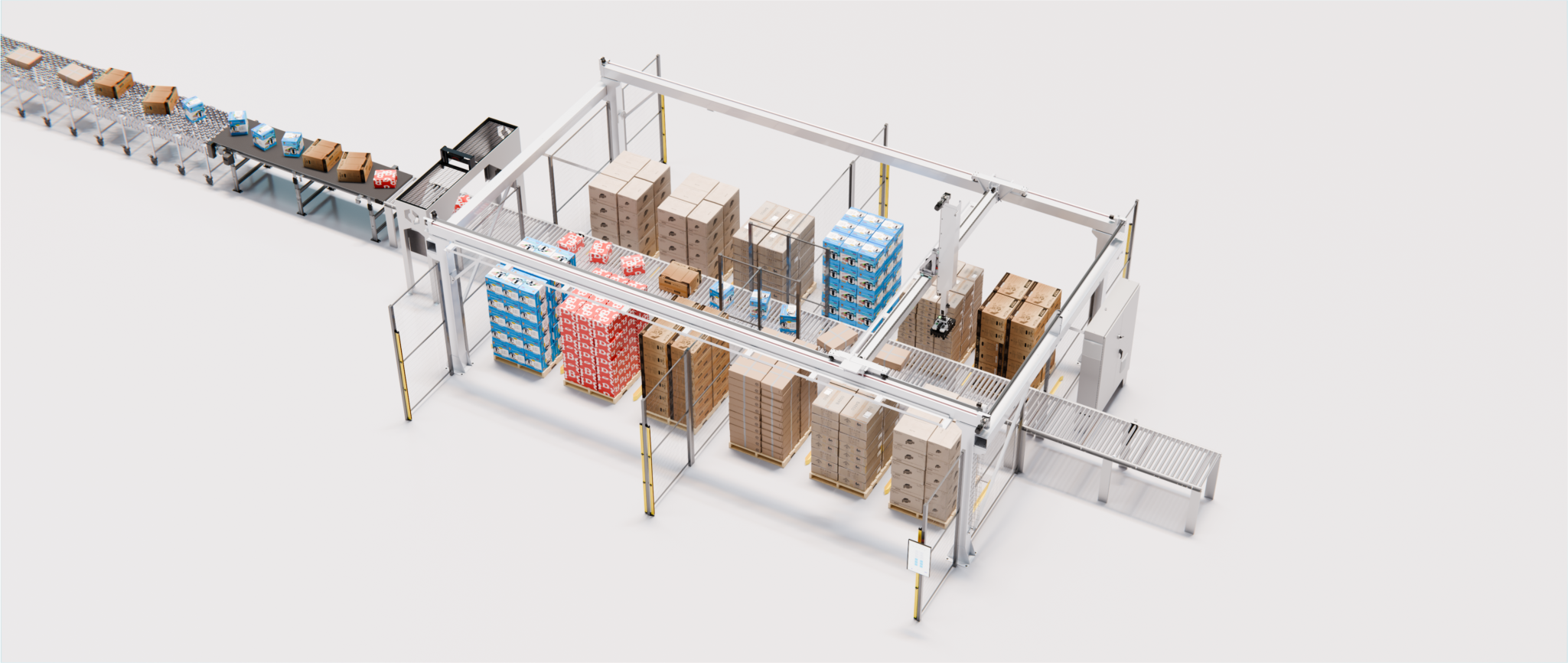
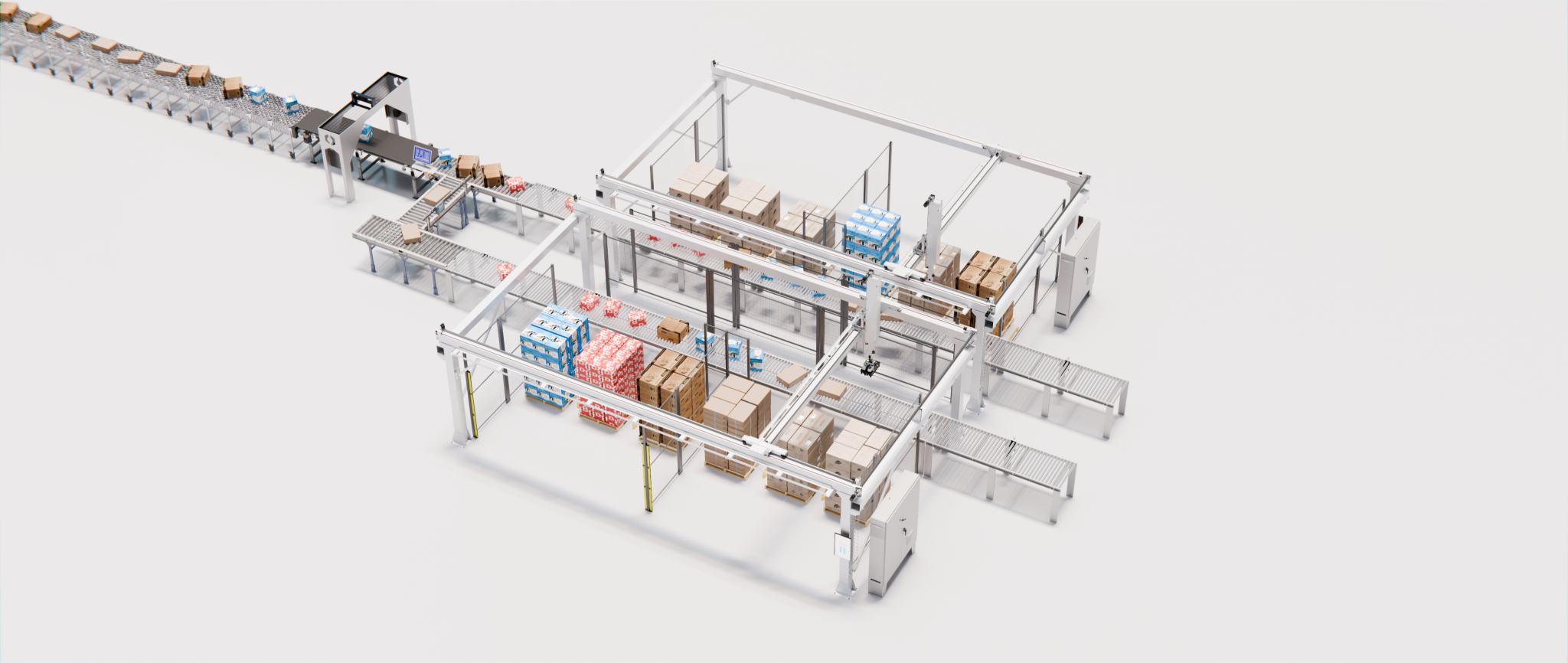
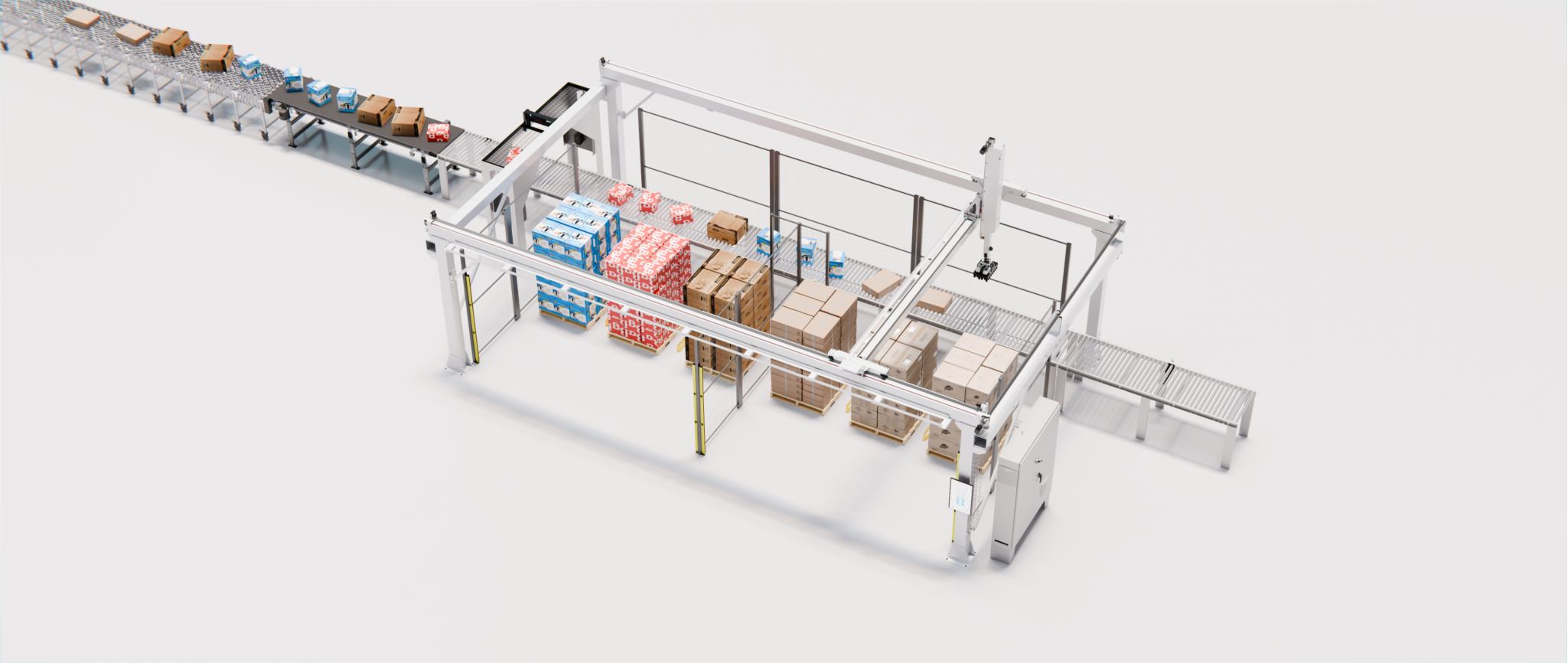
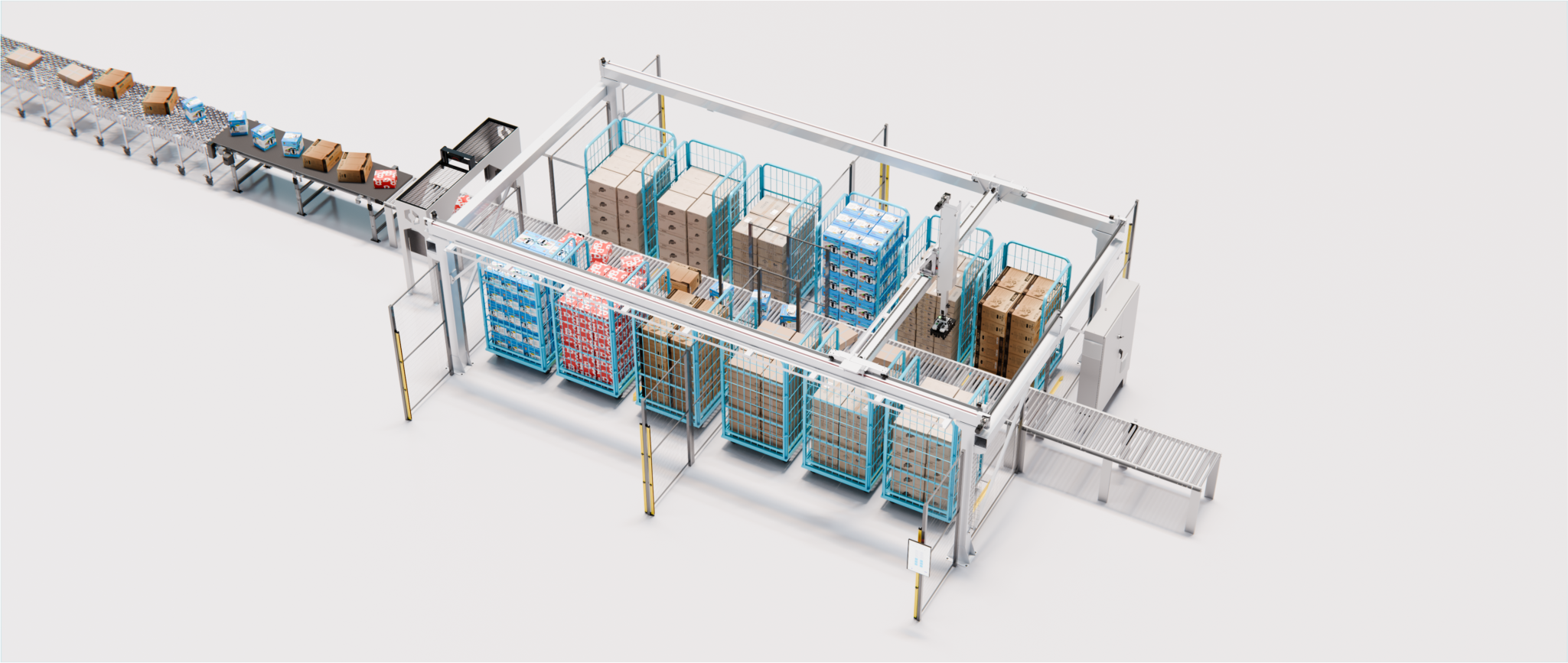
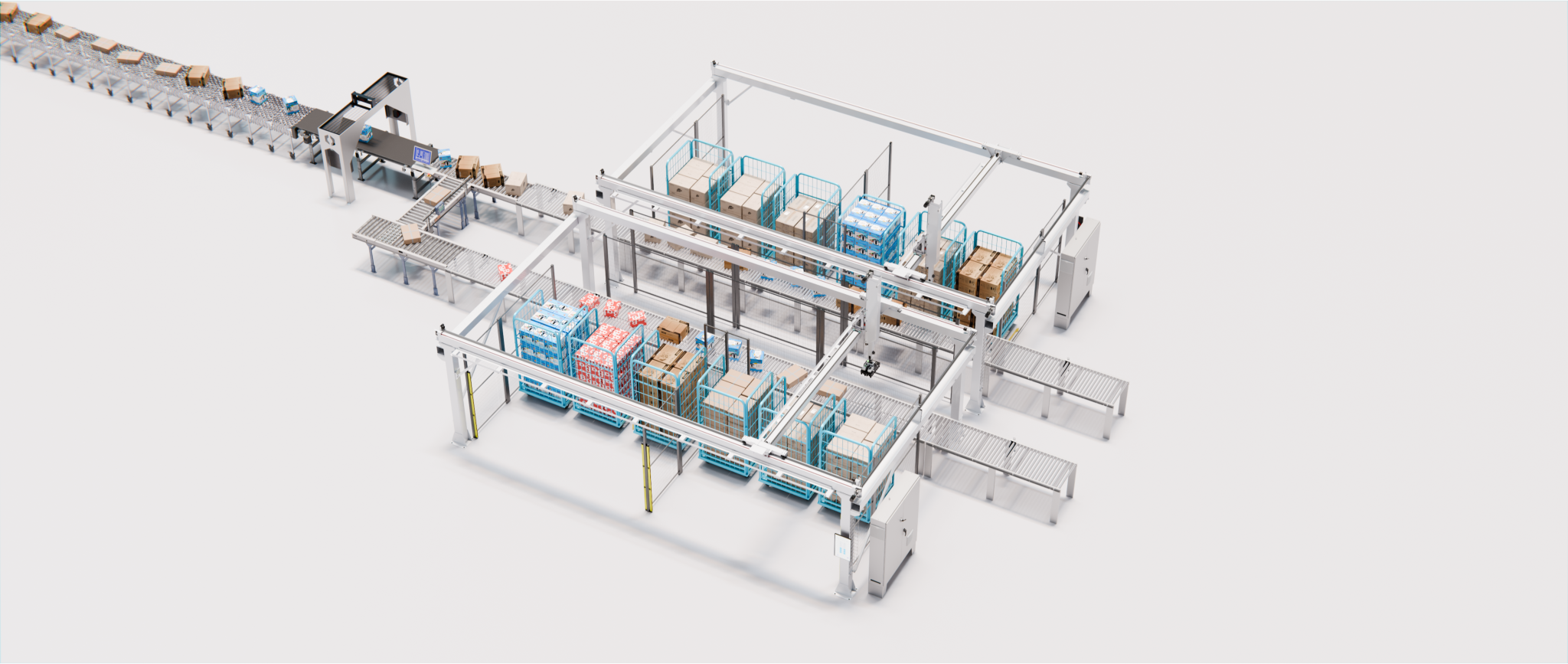
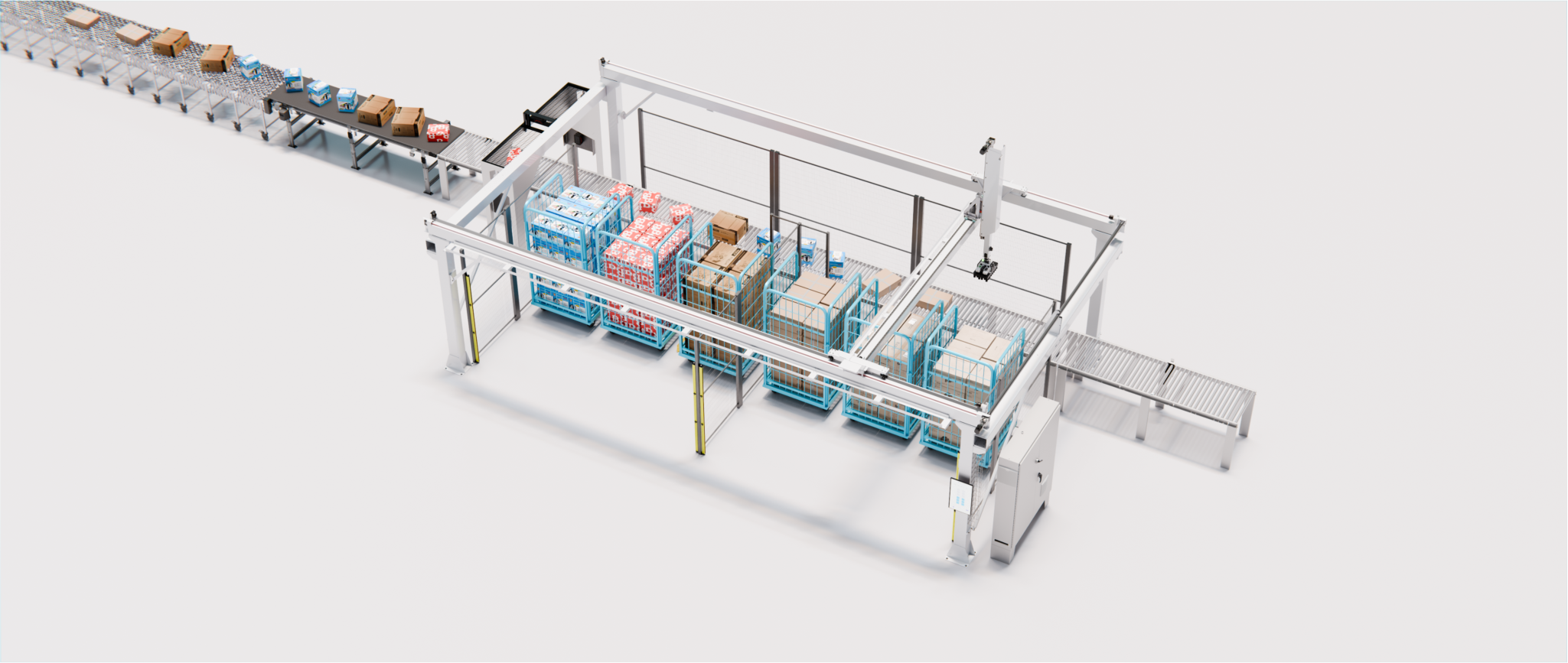
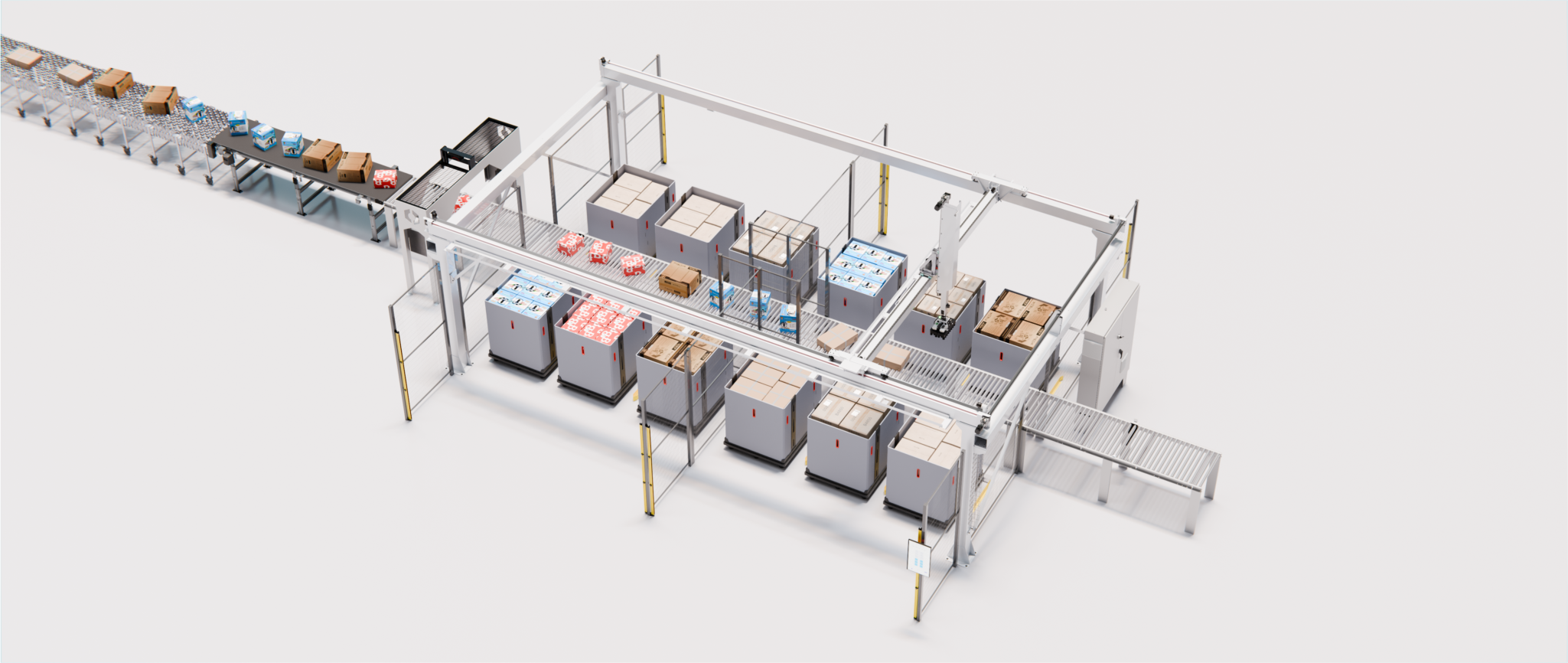
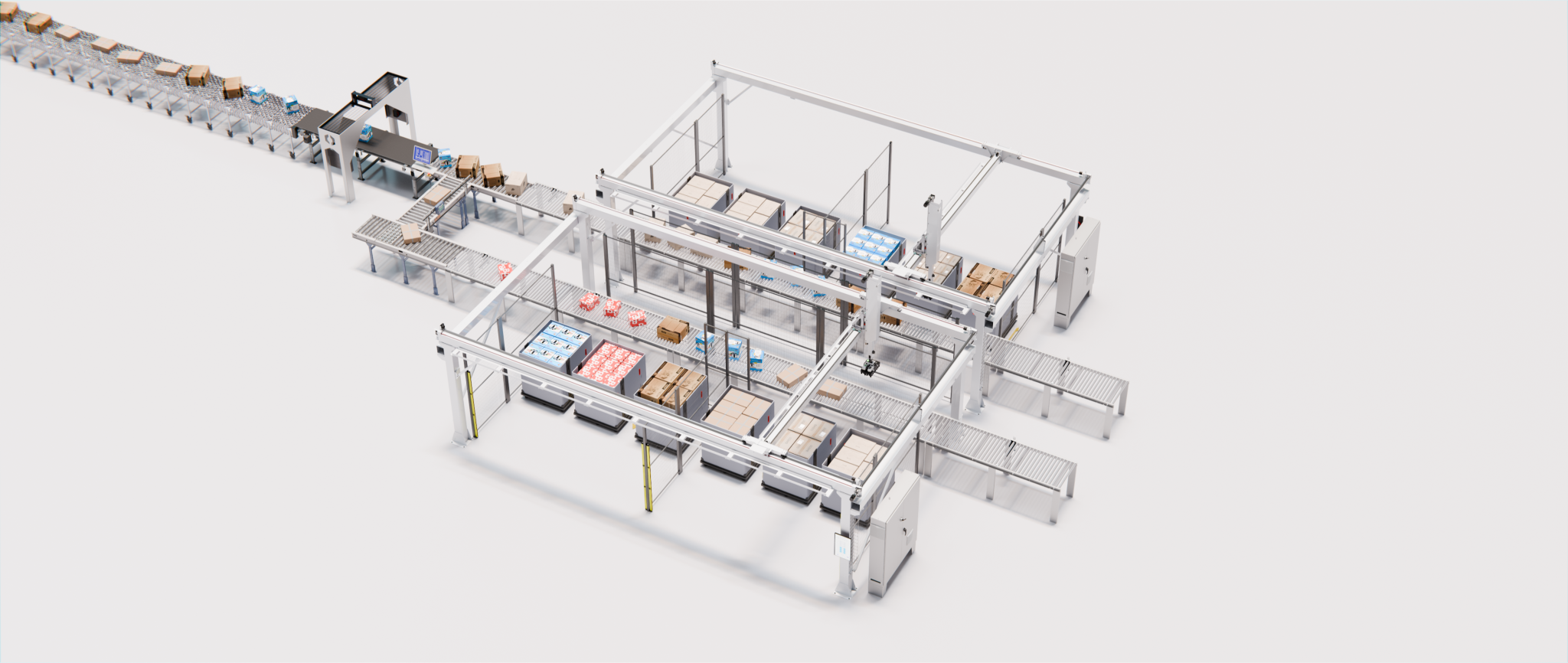
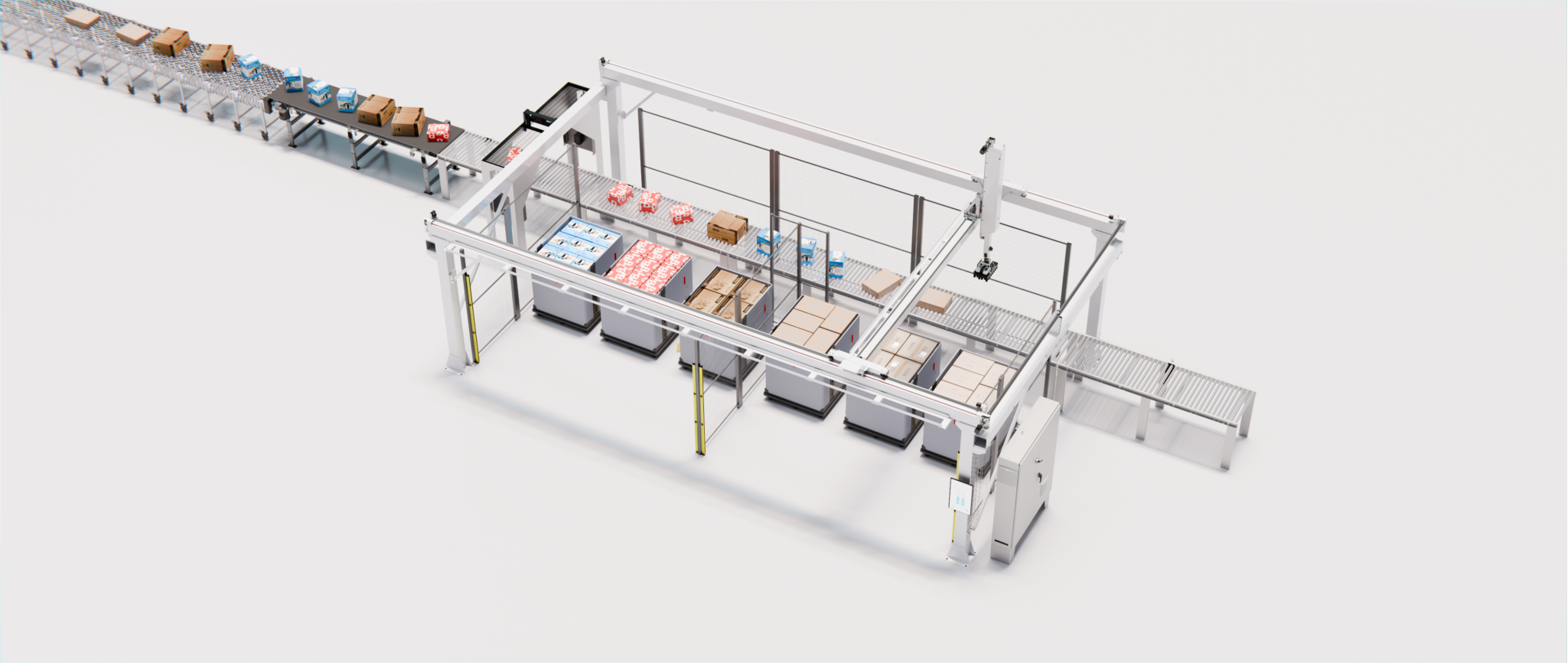
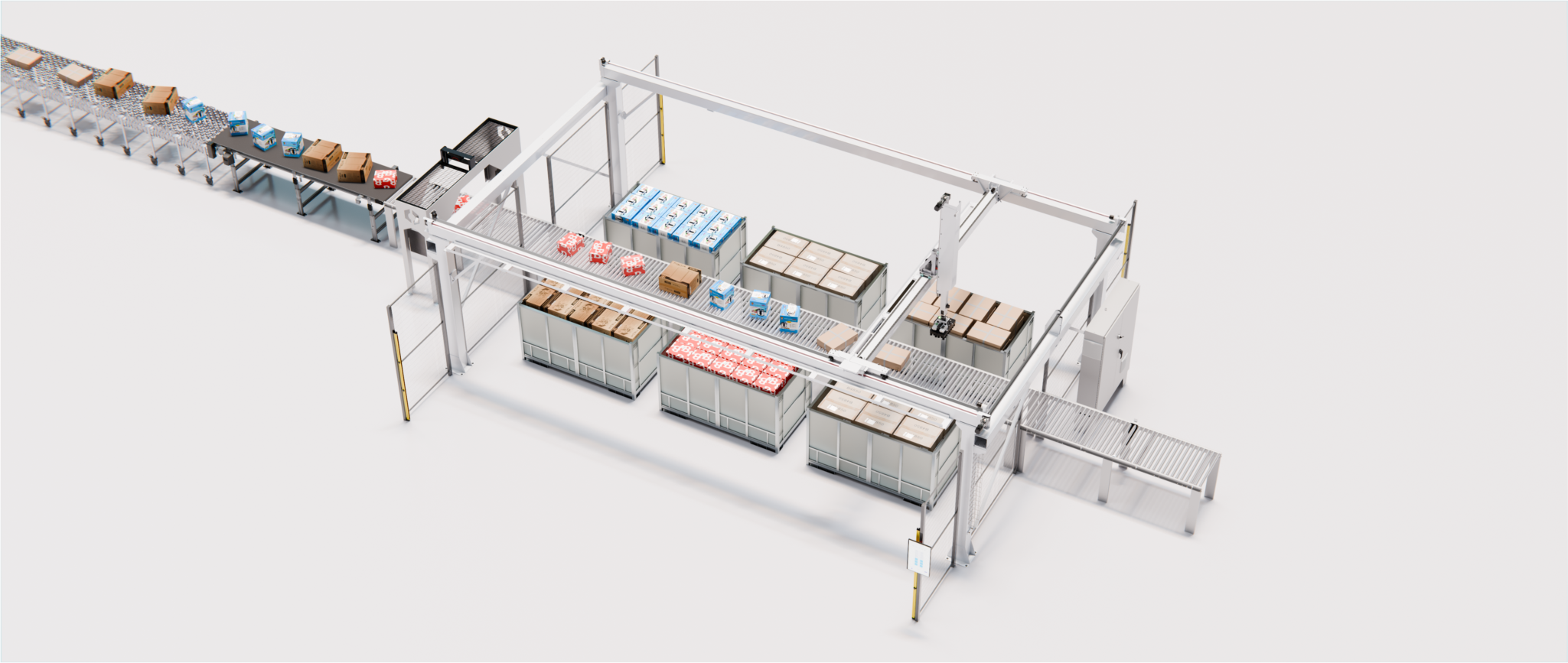
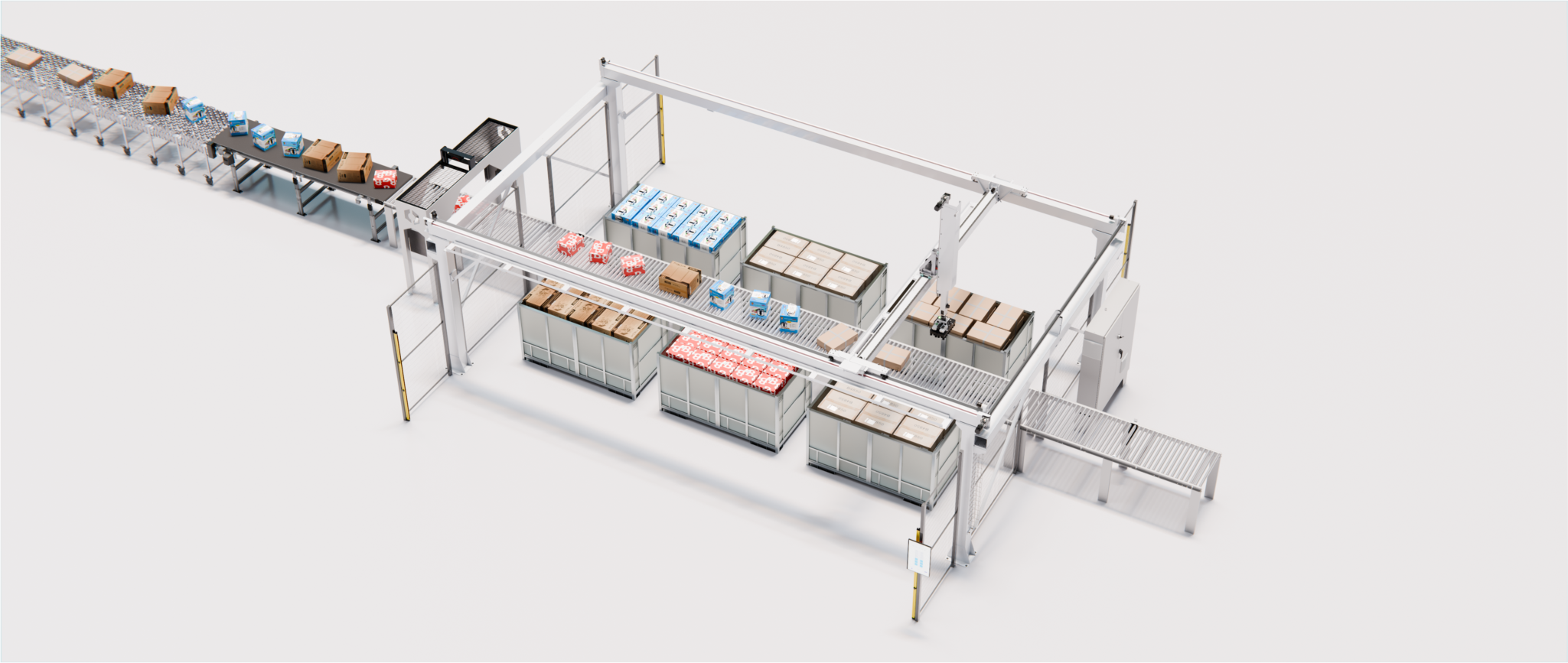
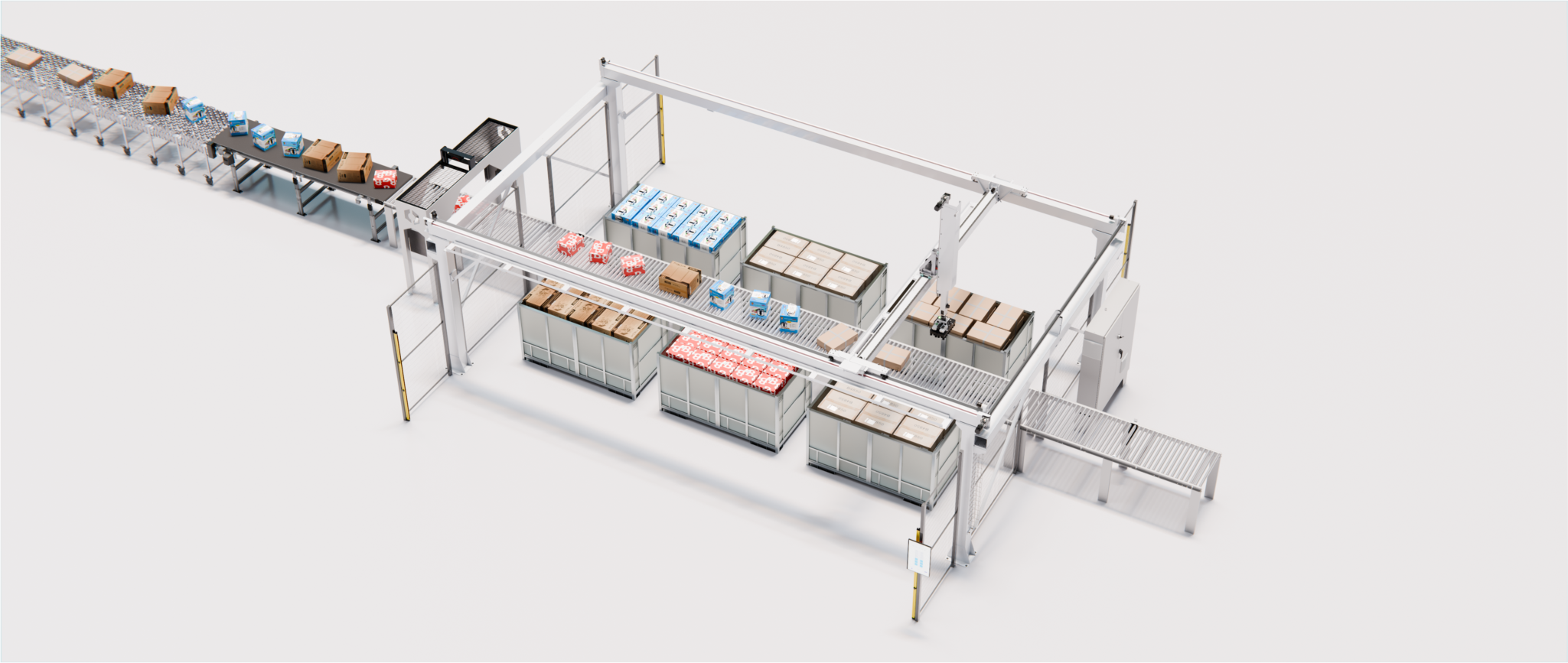
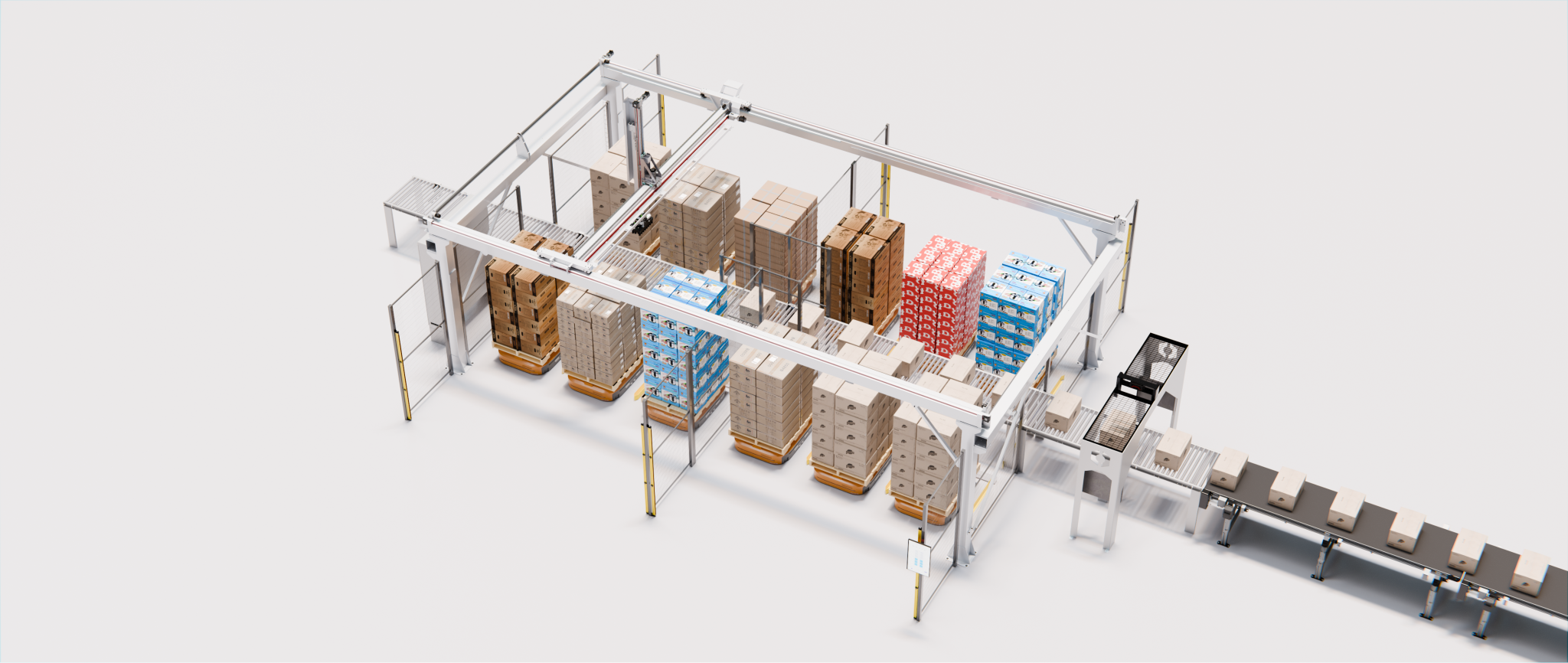
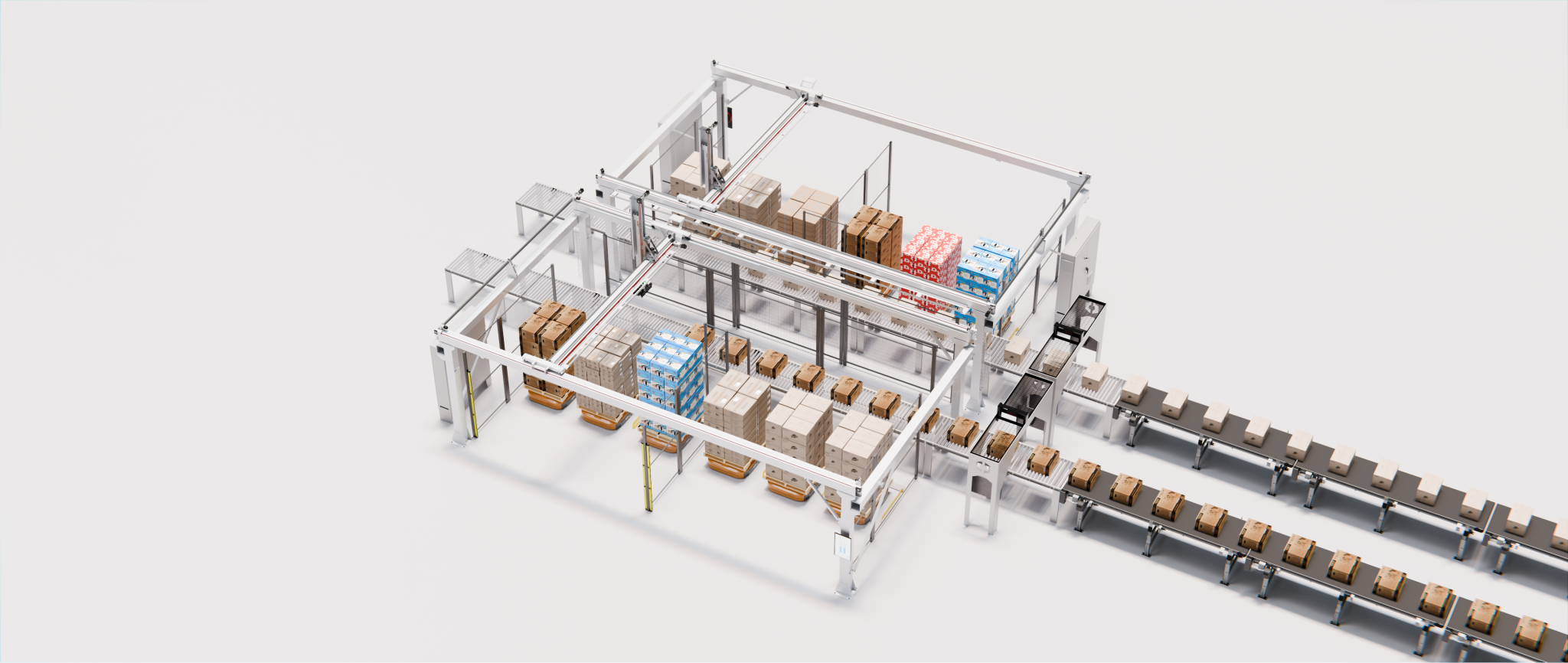
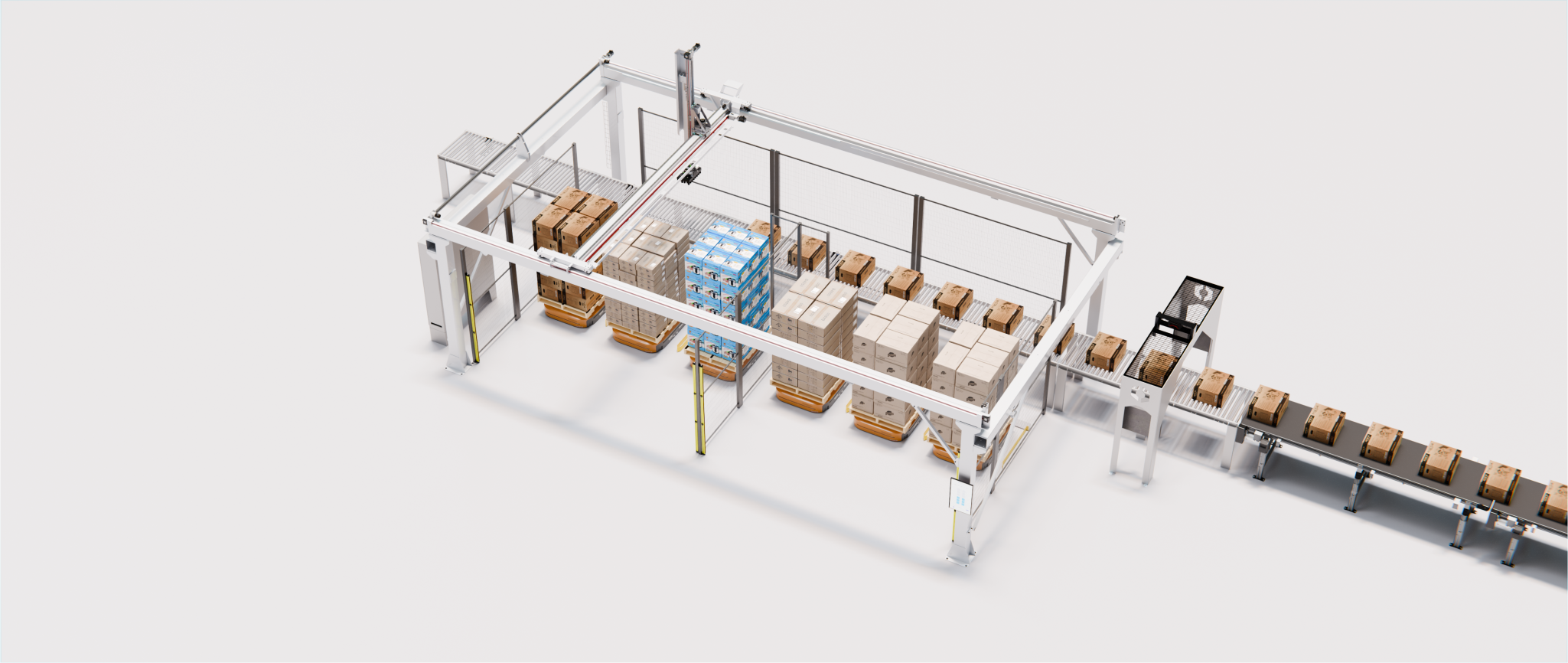
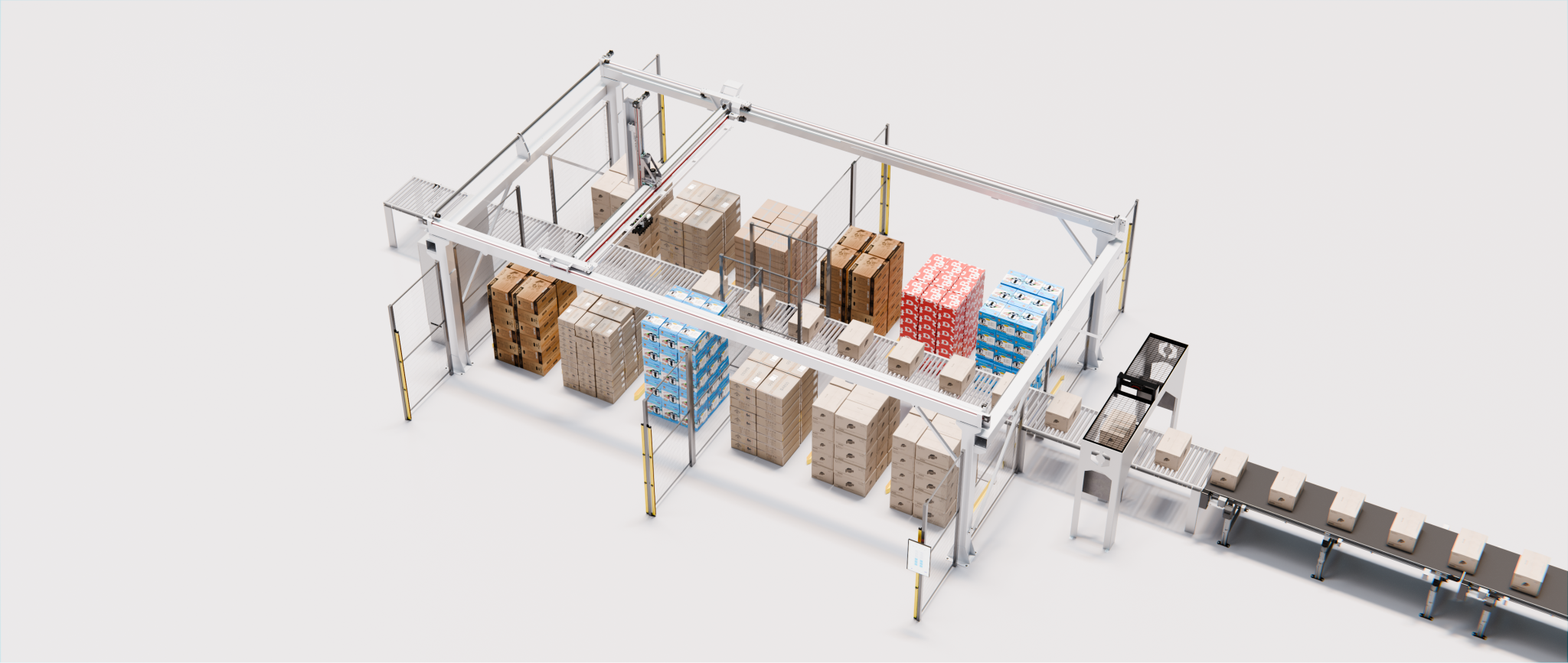
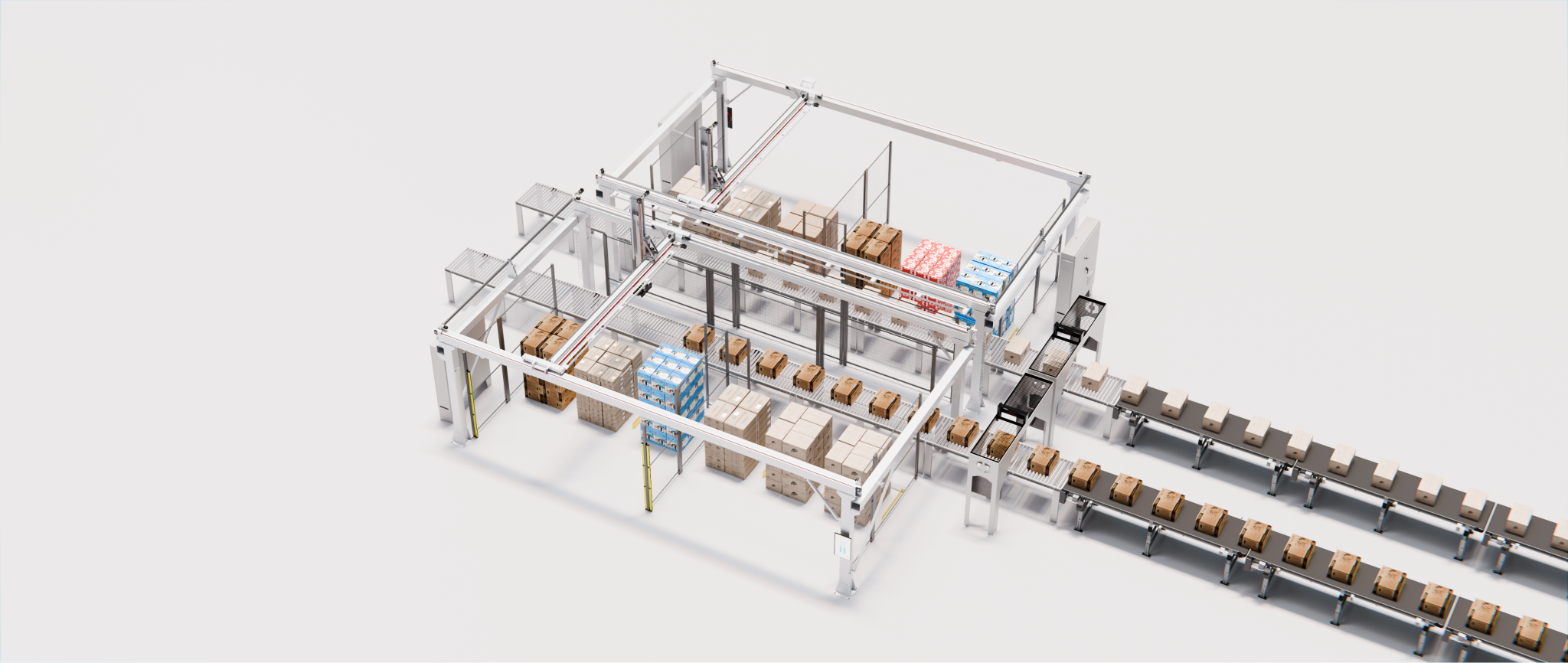
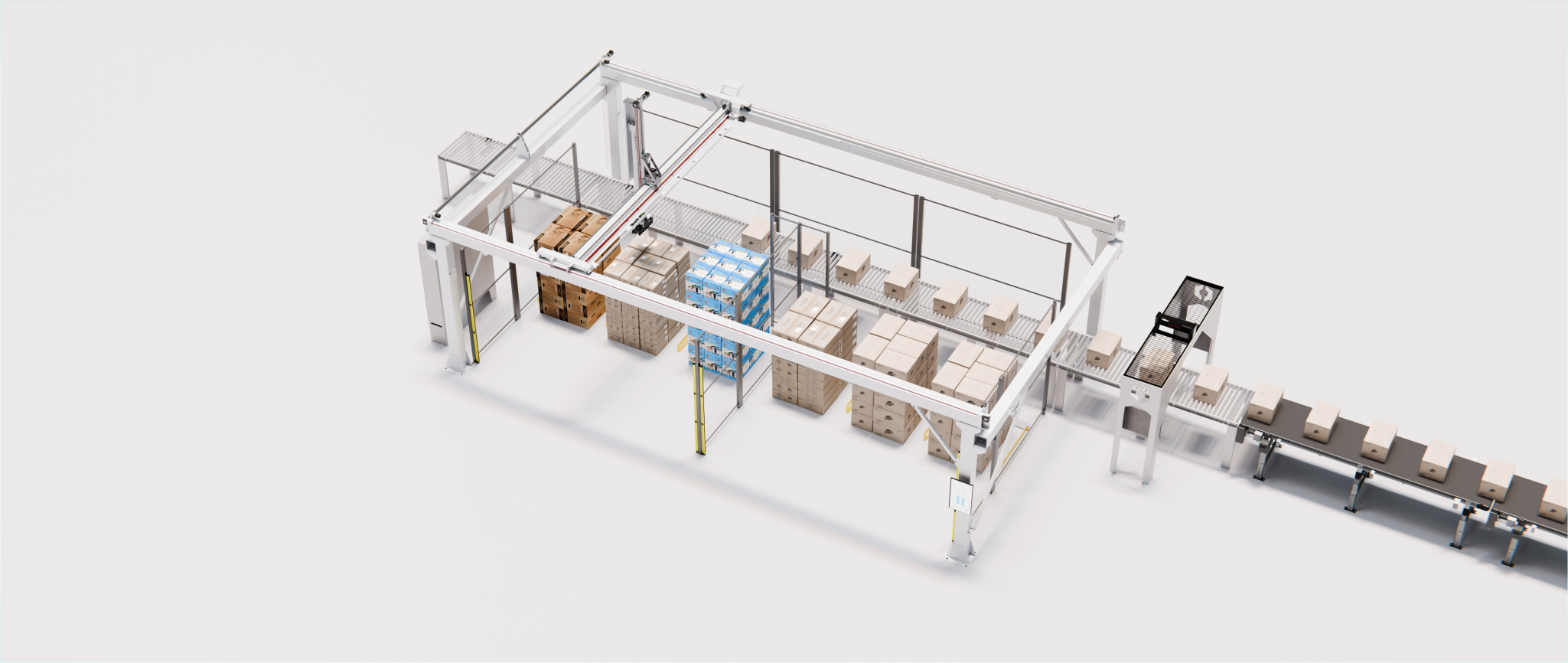
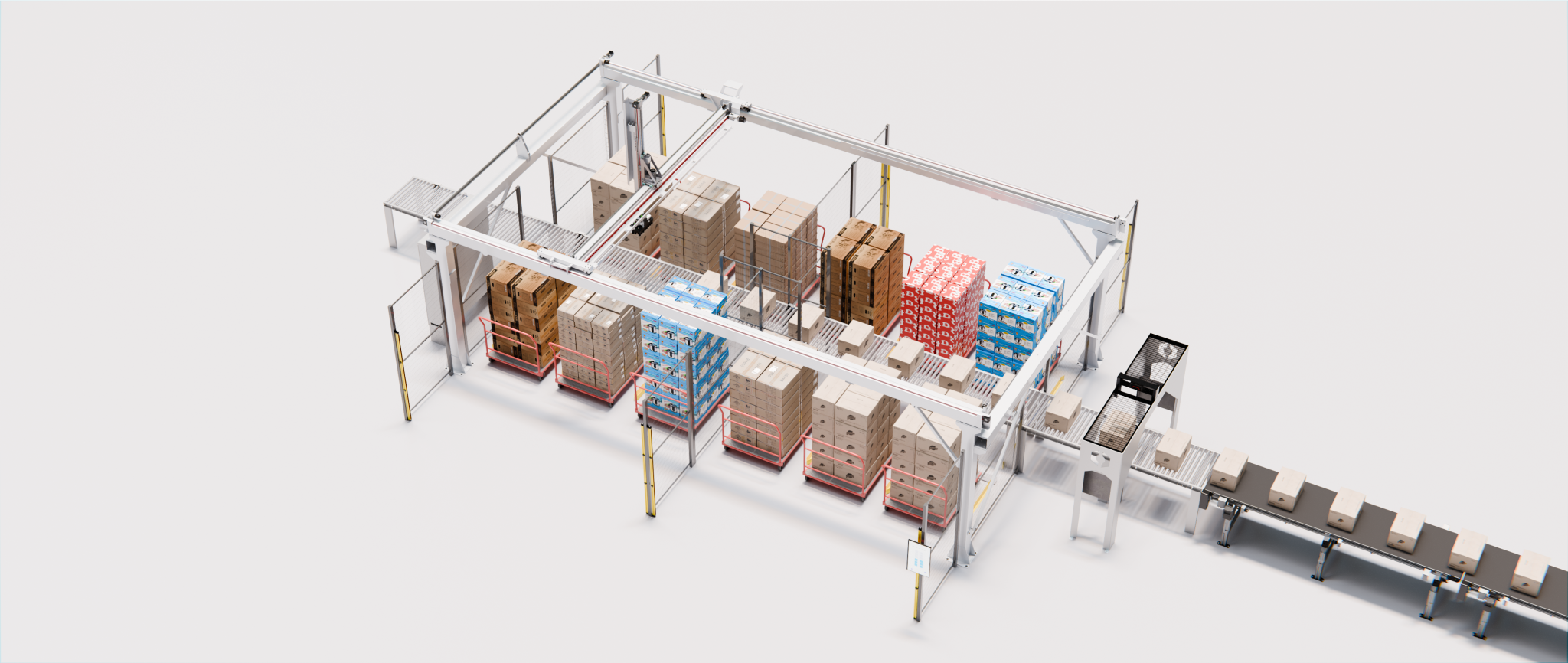
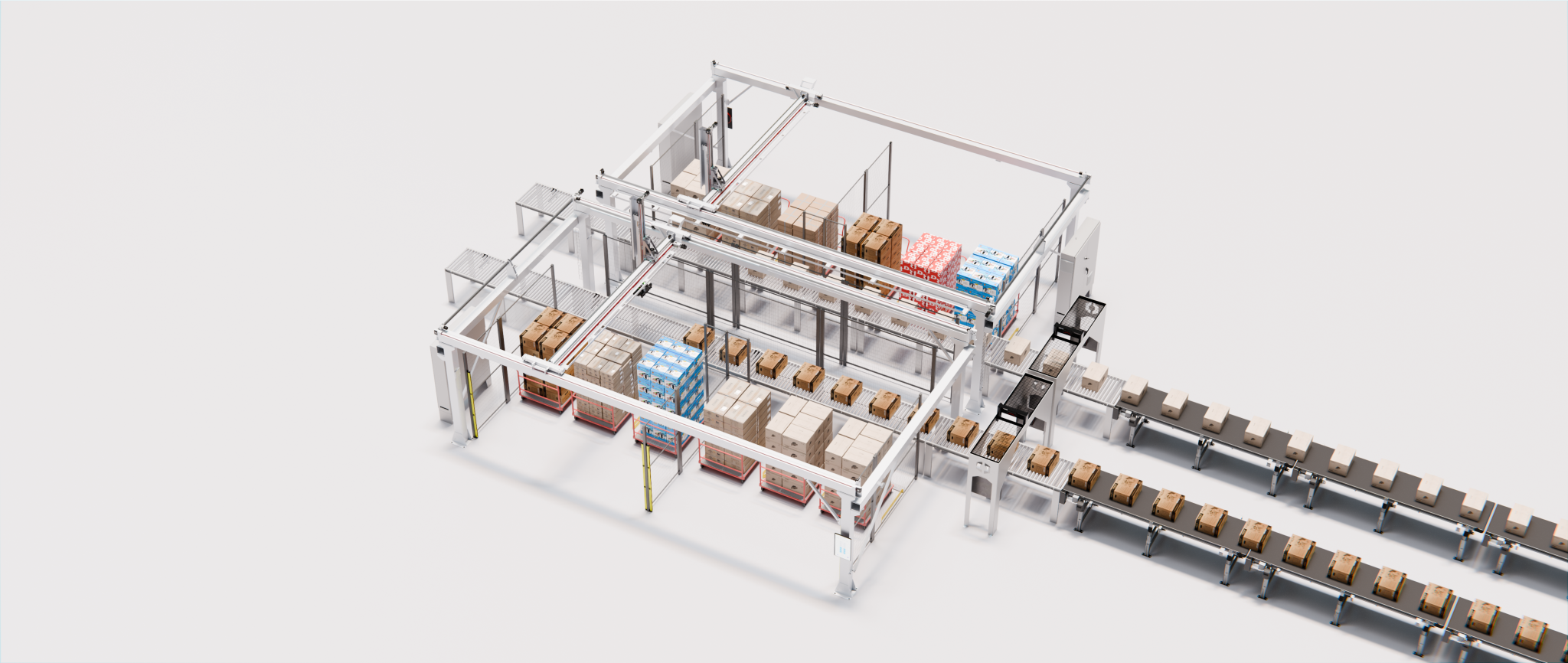
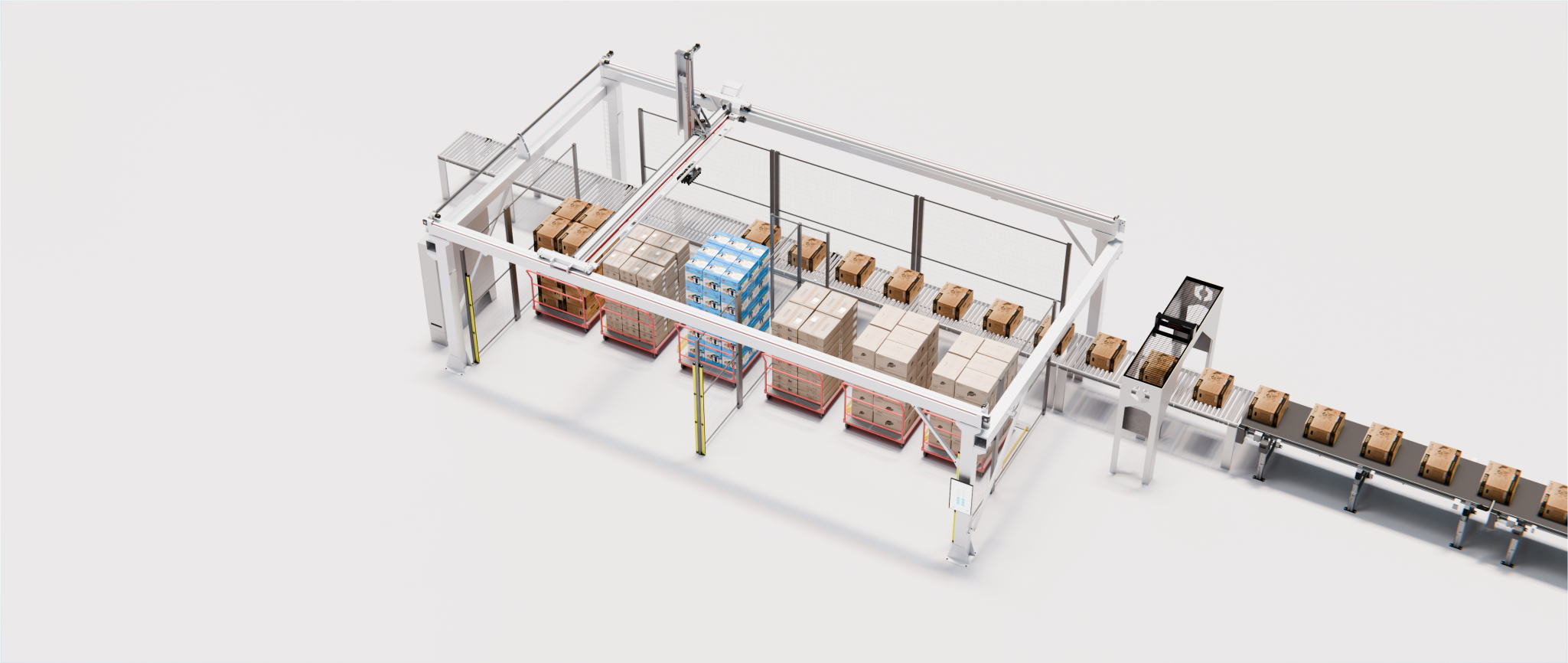
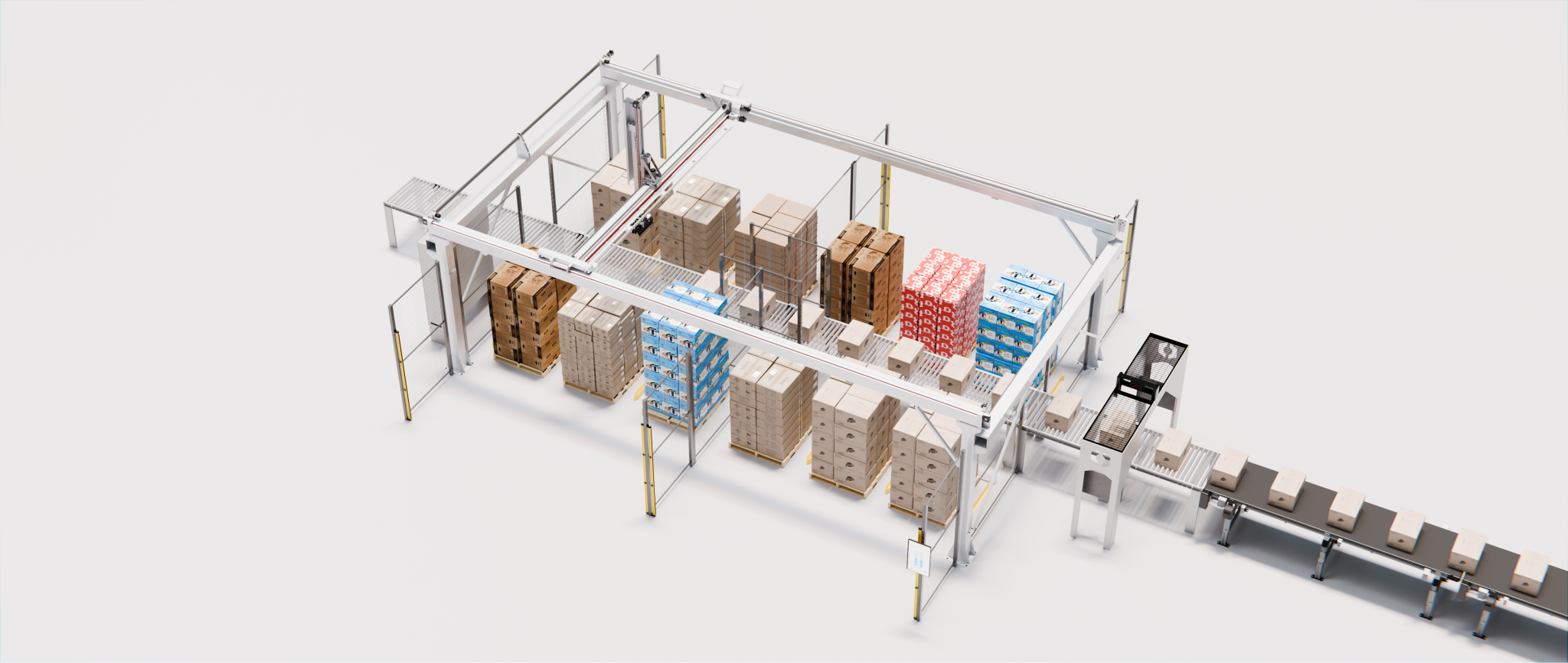
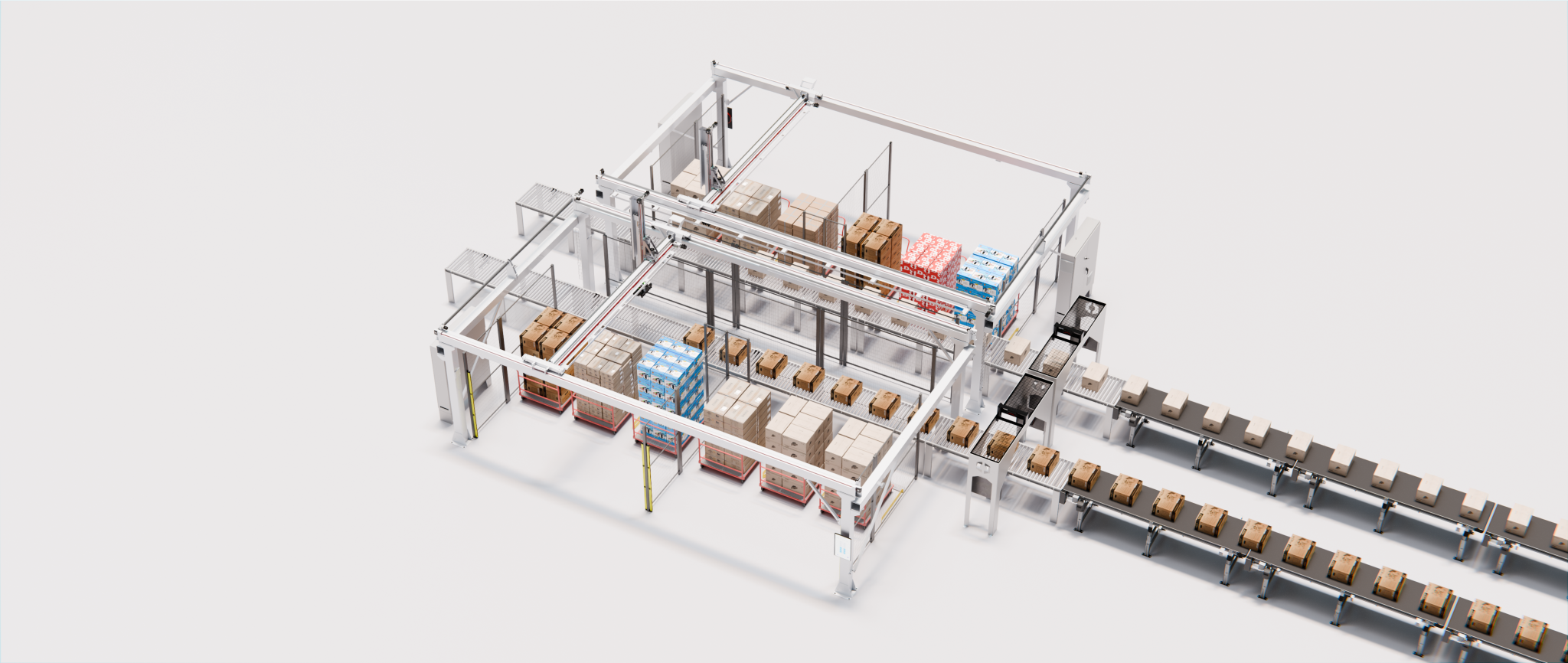
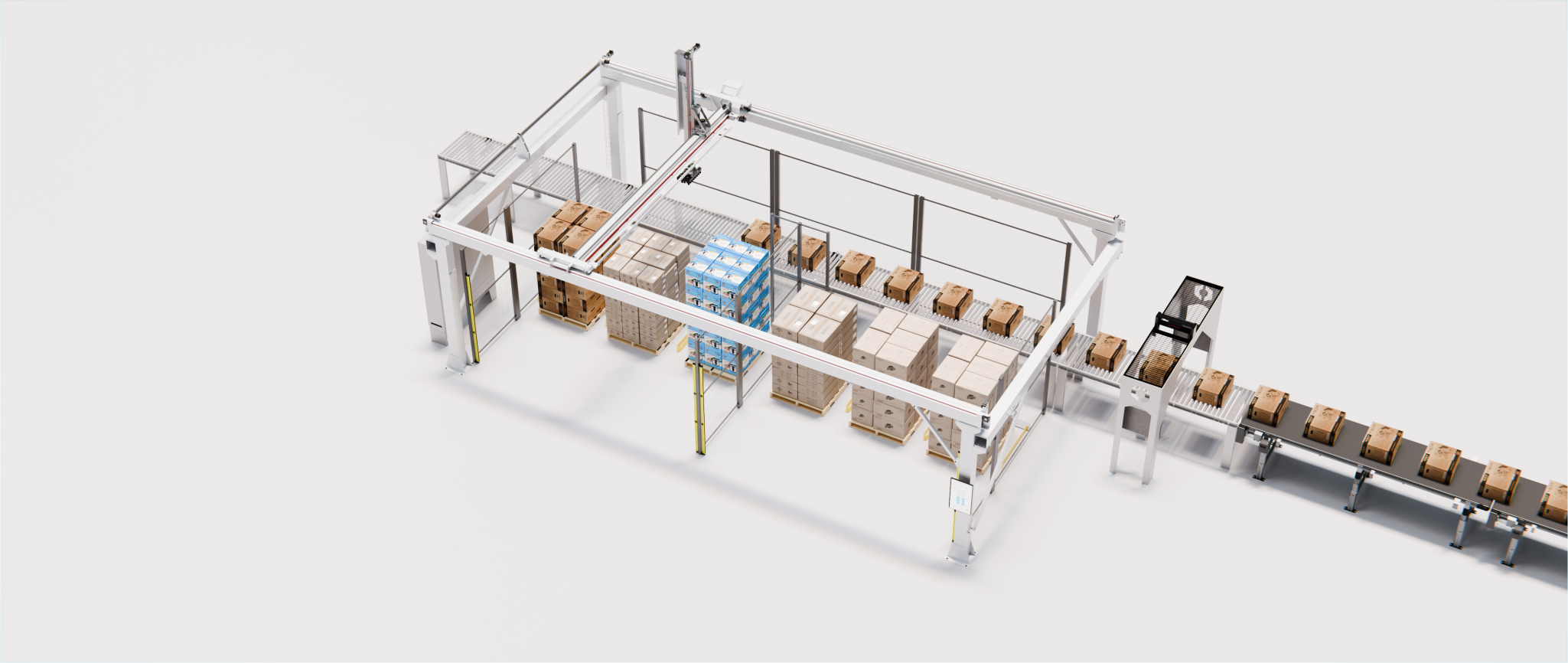
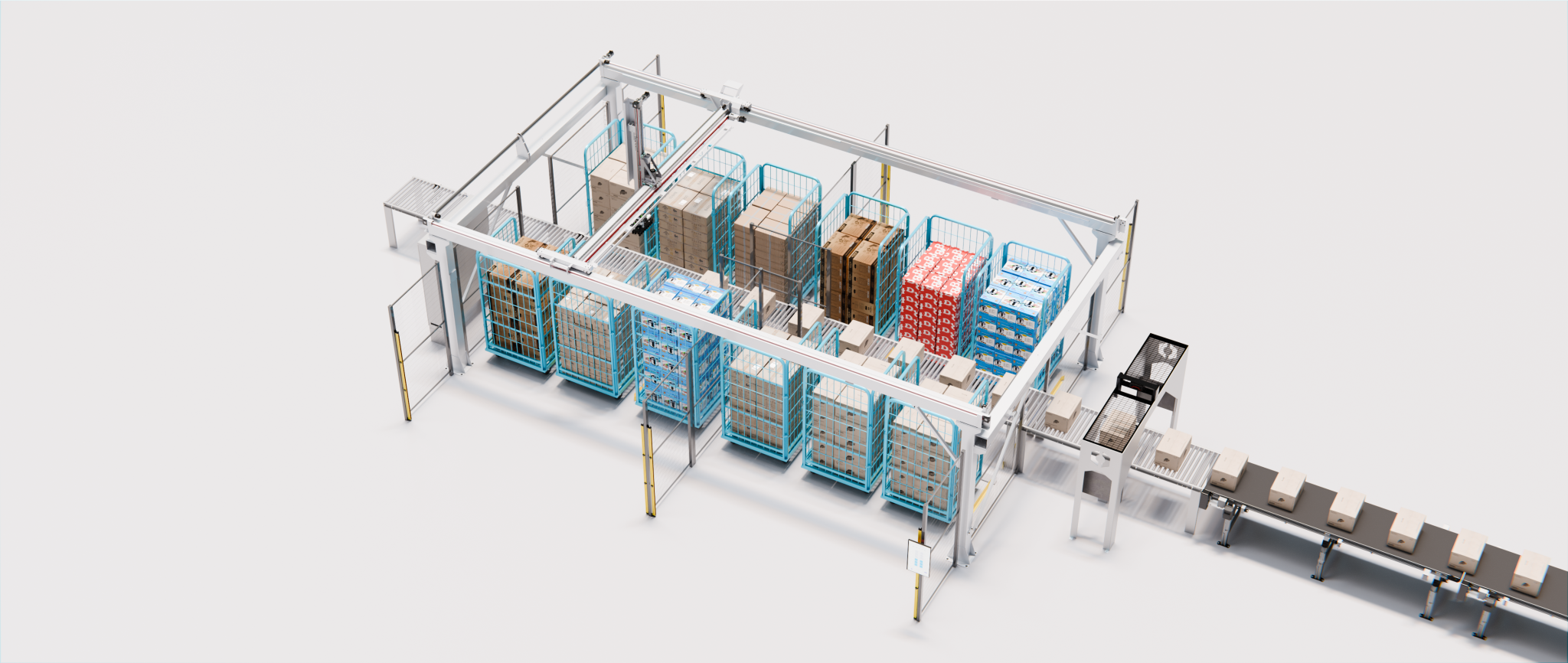
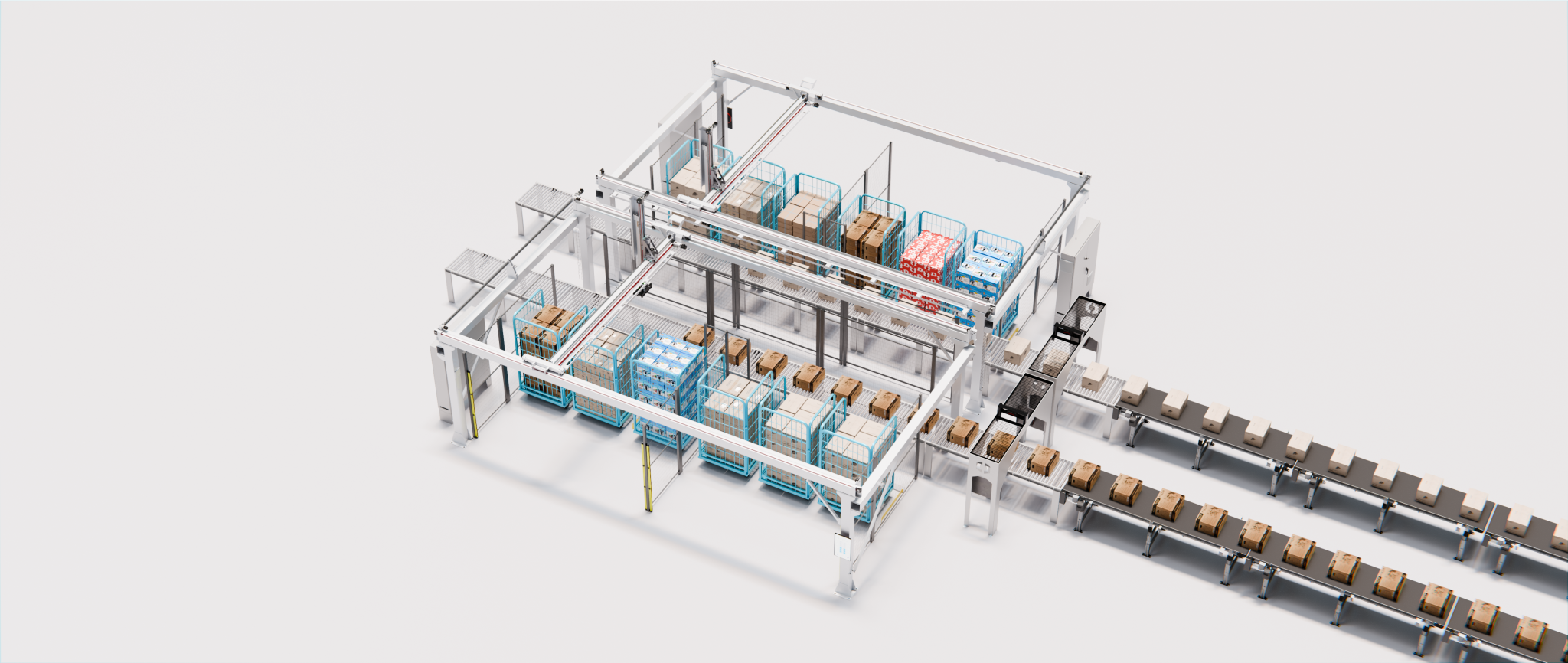
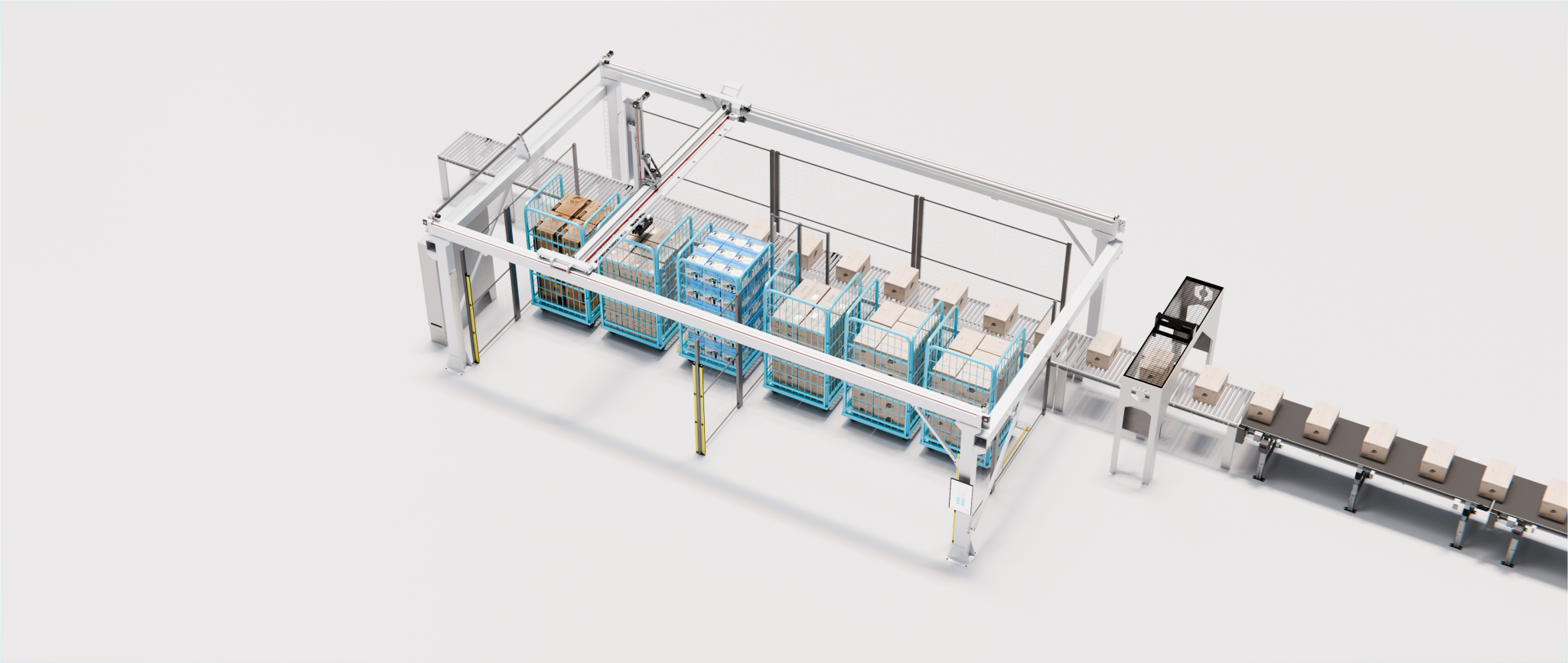
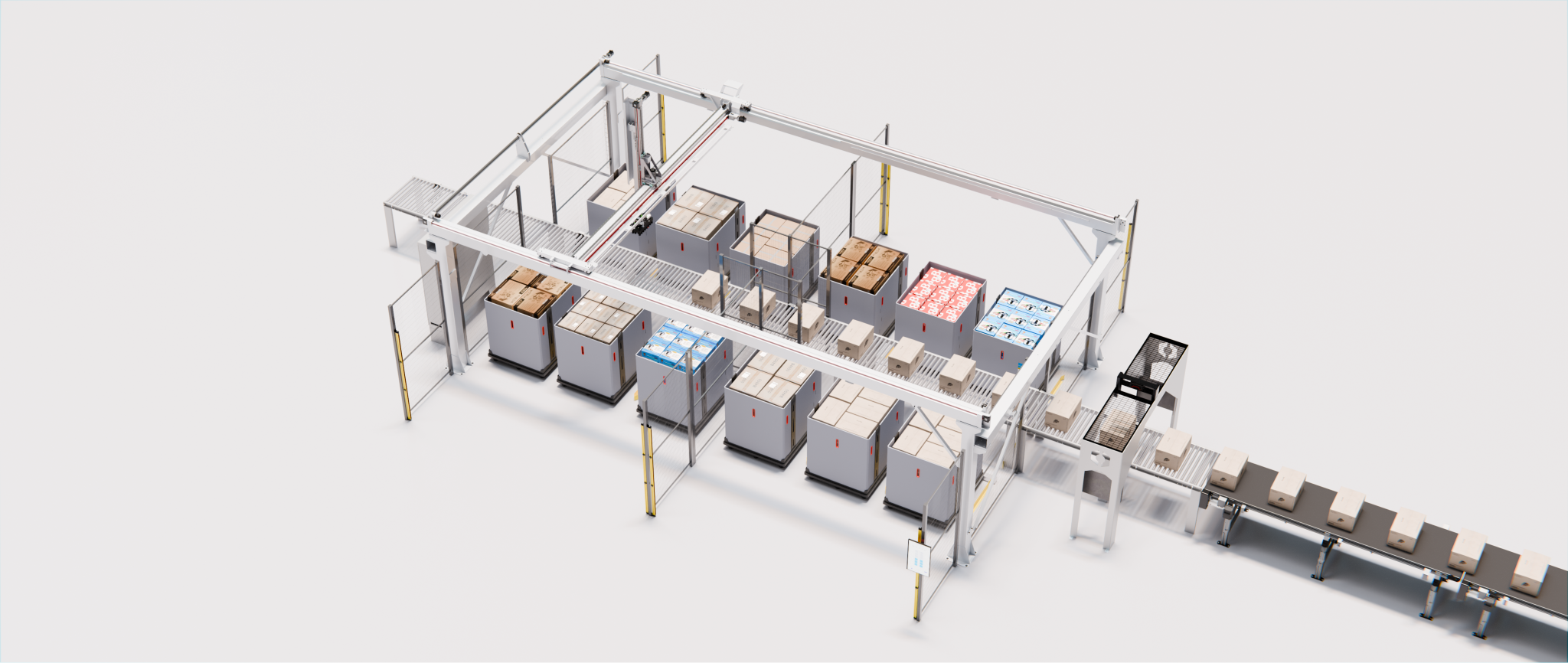
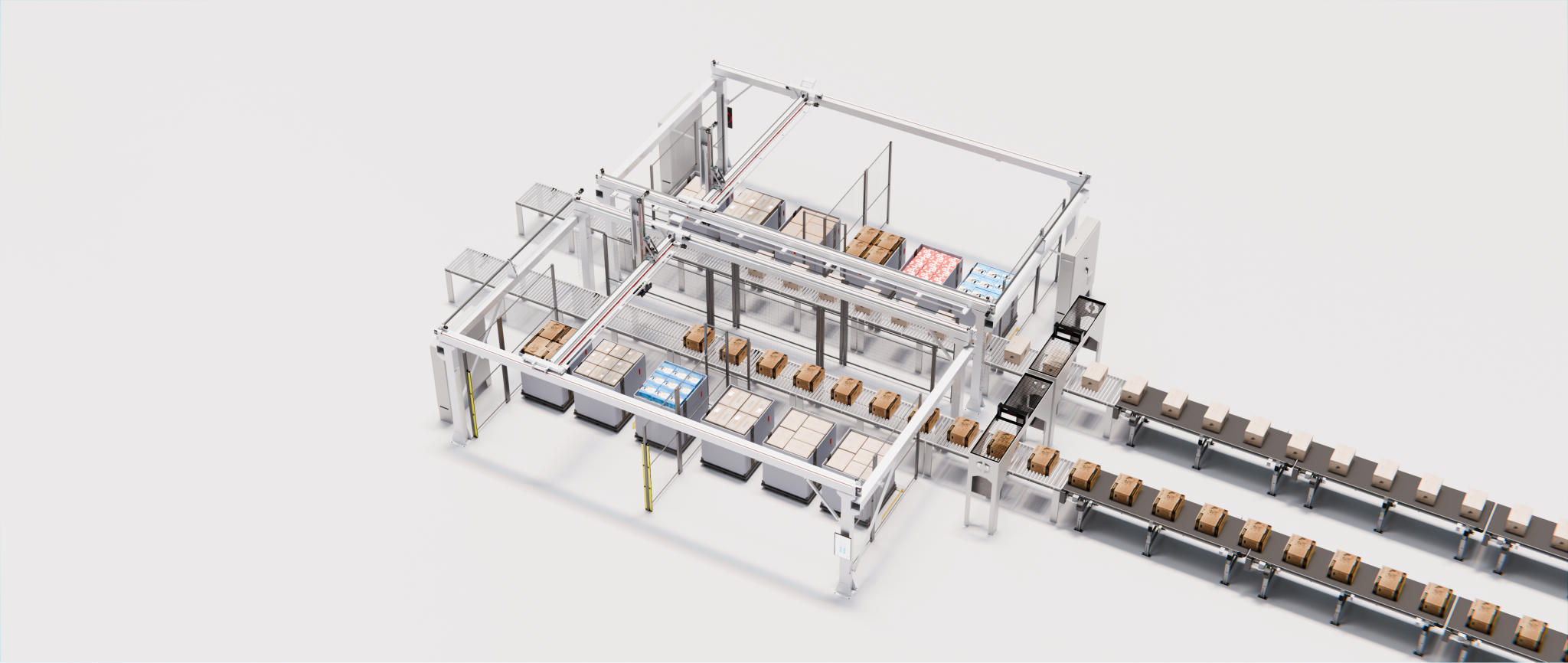
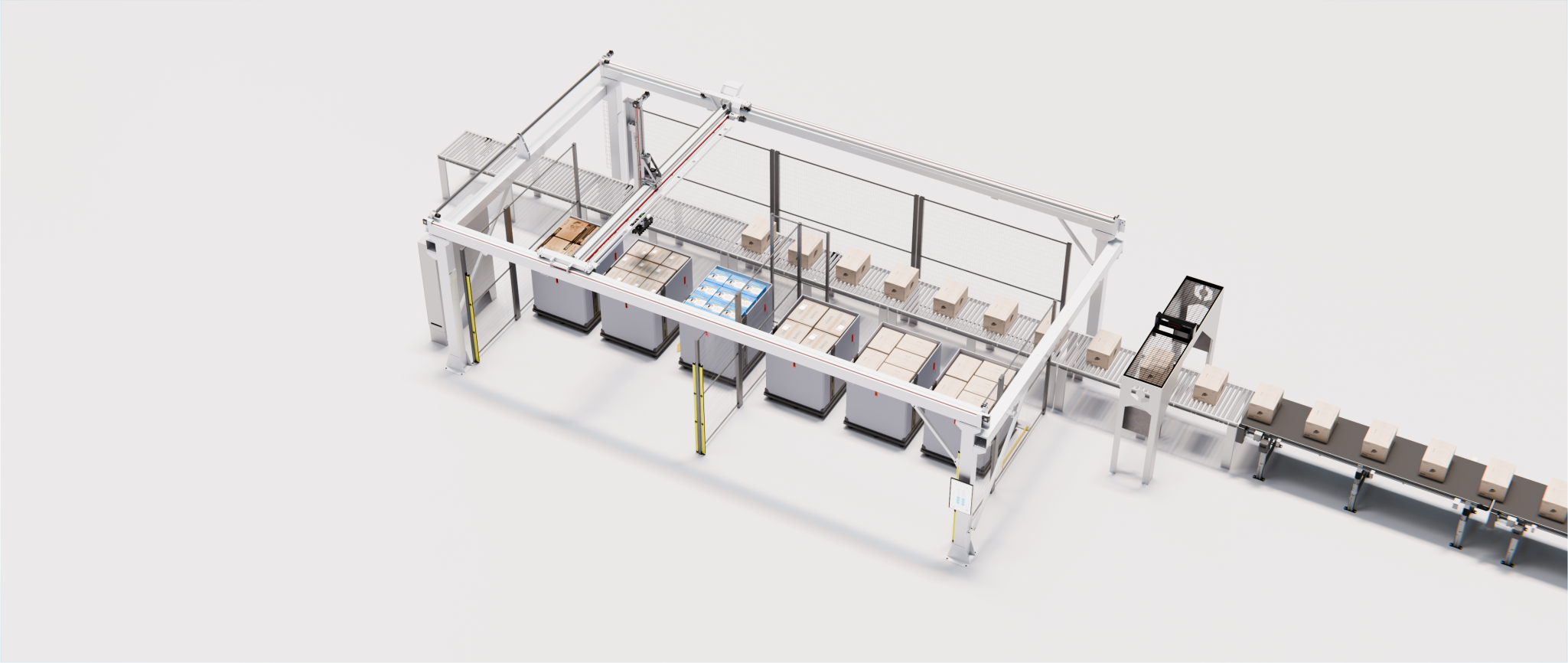
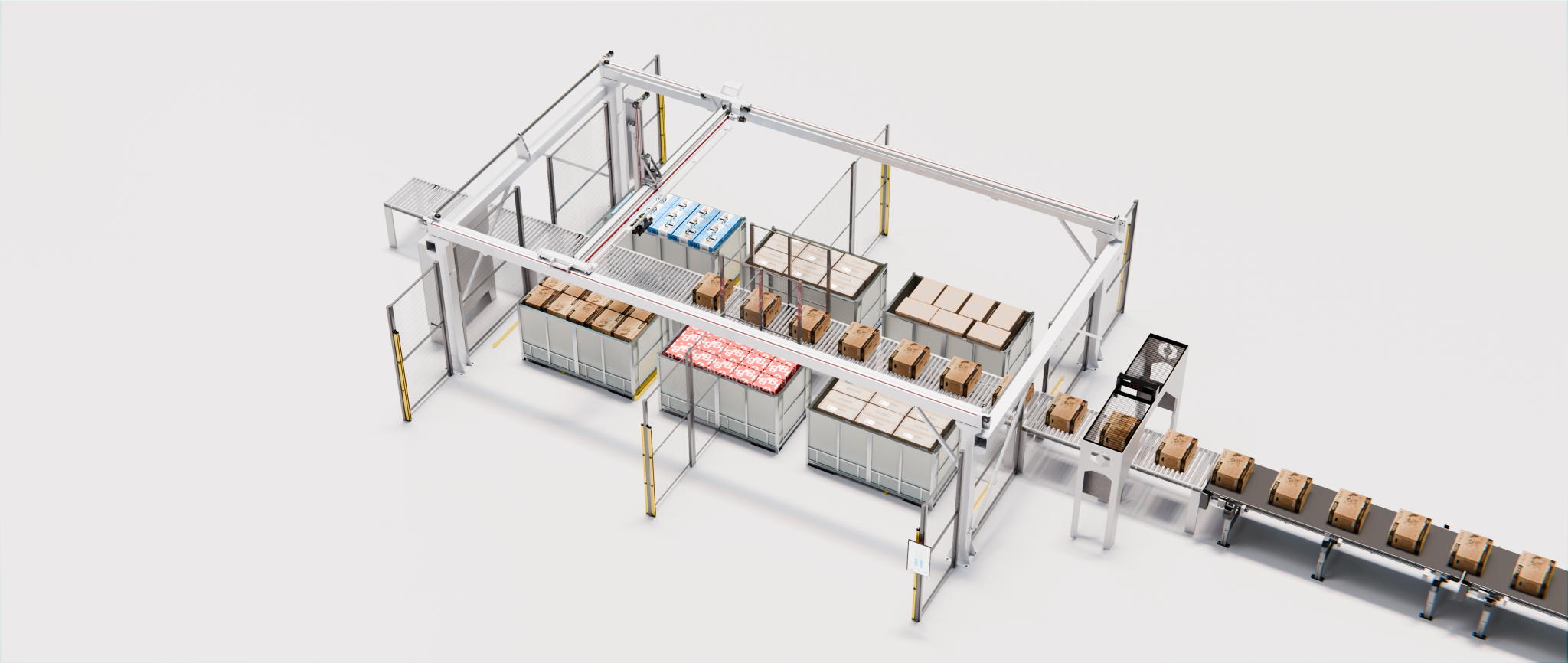
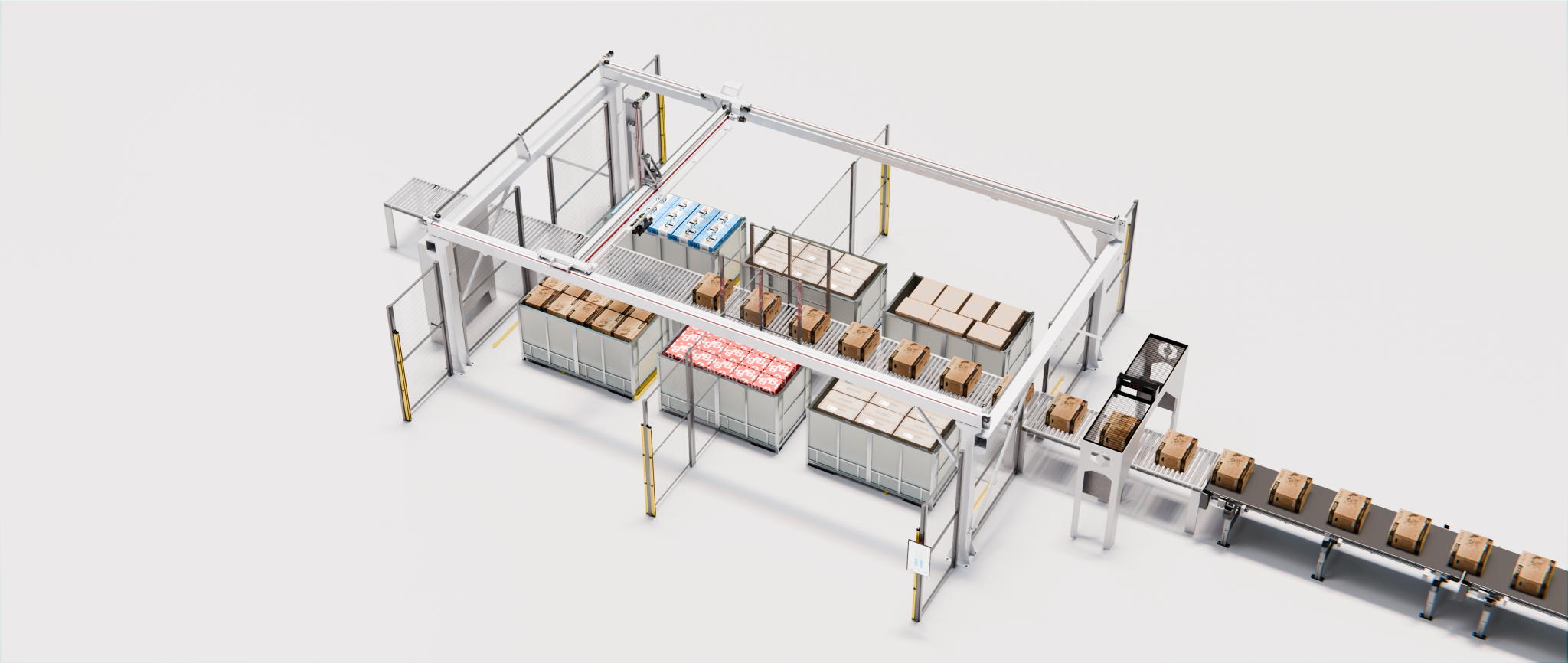
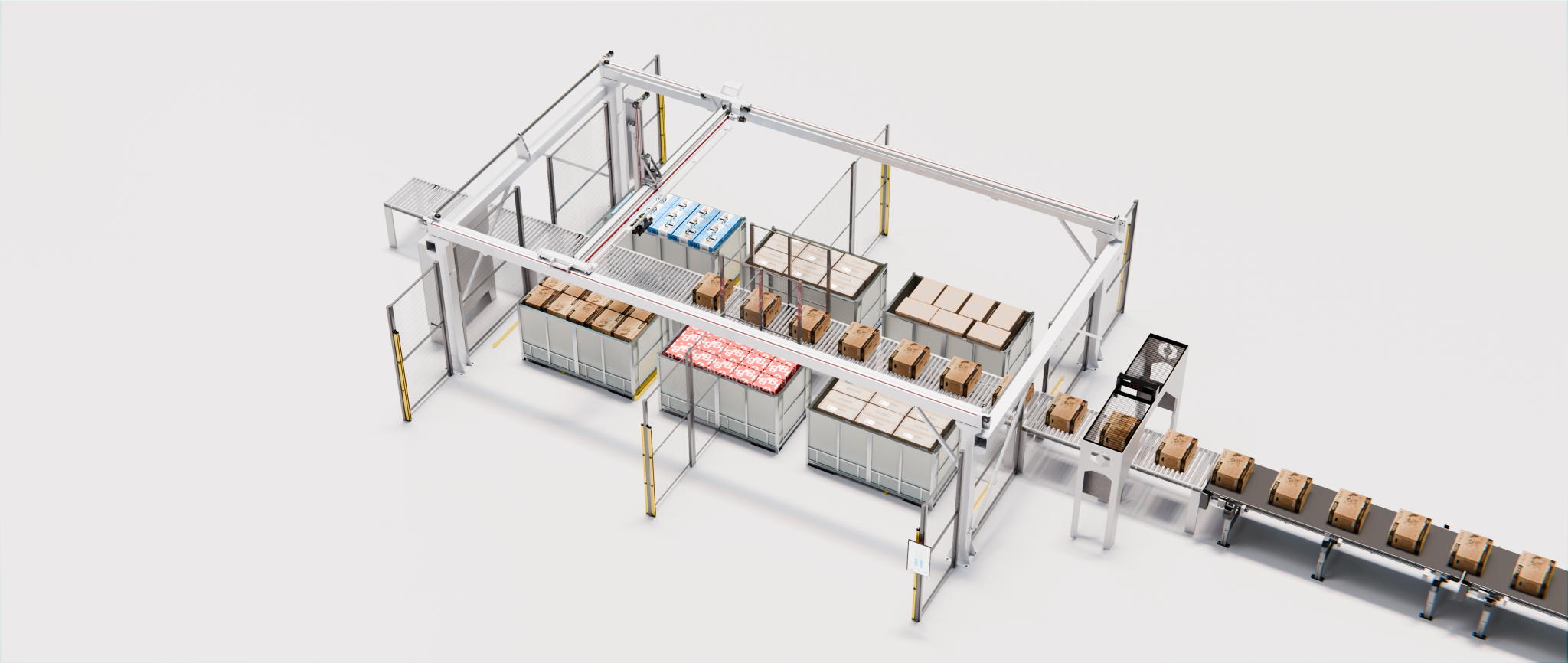
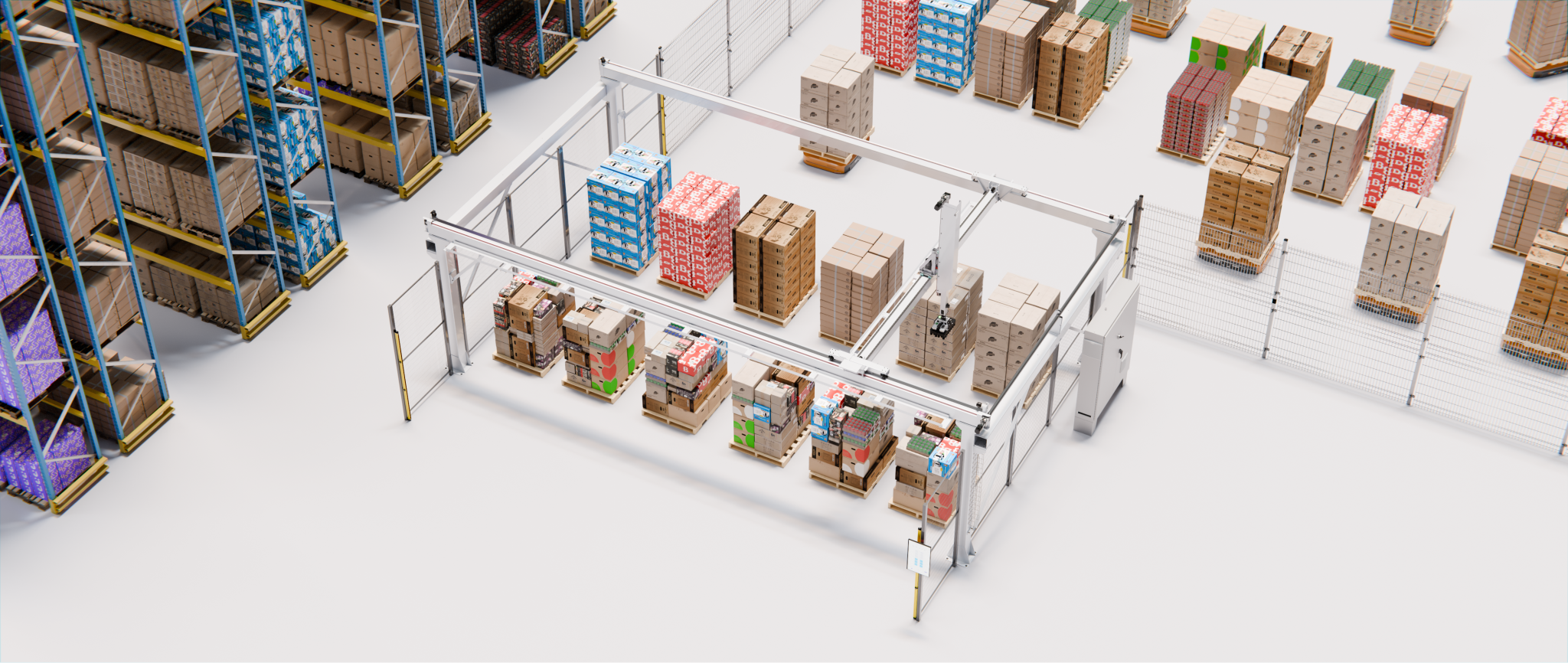
Build your AmbiStack system today
AI stacking technology like you've never seen
Sim2Real RL
AI-Powered Vision
PRIME-1
Tap into productivity
-
Smart Notifications
Stay informed with real-time alerts for optimal uptime. View full pallets, monitor targeted pallets, and receive notifications to replace or replenish complete stacks.
-
Real-Time Analytics
Track performance in real time with detailed charts and data-driven insights. Monitor key metrics like throughput, errors, exceptions, sort times, and output heatmaps, while easily tracking time and optimizing throughput across your entire fleet.
-
Training Hub
Access video tutorials, system guides, and comprehensive training for smooth onboarding and continuous learning.
We sort it out. So you don't have to.
-
Spare parts program
Onsite and on-demand spare parts to minimize downtime.
-
Software updates
Real-time updates ensure robust, reliable data for robotic sorting and stacking.
-
Robot Operator training
Operators are trained to optimize workflows, troubleshoot, and improve sorting accuracy.
-
24/7 Support
Onsite product support engineers ensure operational excellence around the clock.
-
AmbiAccess
Monitor robotic fleet performance, review analytics, and access 24/7 support in one platform.
-
Inventory Promise
Best-in-class hardware, always on hand to ensure you get what you need, on time.
We'll show you how the savings stack up
Get in touch with sales
Explore parcel sorting solutions
AmbiStack in the news
-
Newsroom | 01.28.2025Watch: Berkeley robotics startup shows off its latest techA Berkeley startup called Ambi Robotics has unveiled its latest innovation: AmbiStack. Co-founder and CTO Jeff Mahler offer details of how the robots work.
-
Newsroom | 01.28.2025Ambi Robotics built a clever solution to automate pallet packingUC Berkeley spinout Ambi Robotics announced Tuesday the arrival of AmbiStack, a novel system that automates pallet packing.
-
Newsroom | 01.28.2025Ambi Robotics launches AmbiStack robotic palletizerAmbi Robotics Inc. today unveiled AmbiStack, an overhead palletizing system designed to stack items onto pallets or into containers.
Questions? Answers.
-
What is AmbiStack?
AmbiStack is a multi-purpose AI-powered robotic stacking system that optimizes sorting and stacking in material handling operations from retail distribution to order fulfillment to shipping.
-
How does AmbiStack work?
AmbiStack features advanced AI technology which allows the robot to stack items without prior knowledge of their size, position, or appearance. Powered by an AI vision system based on foundation models, AmbiStack analyzes, tracks, and picks each item while performing quality control checks. Its AI planning system, built on simulation-to-reality technology, eliminates the need for tedious real world data collection, allowing rapid deployment into production. This system uses reinforcement learning to reason about how to efficiently stack unseen items to maximize container utilization.
-
Can AmbiStack integrate with my warehouse control system?
Yes, AmbiStack is easy to integrate with warehouse control or management systems. AmbiStack is powered by an industrial PC, which makes custom integrations more straightforward than PLC powered systems. Most information that AmbiStack gathers about the items that are palletized and the pallets that are created can be sent to customer systems.
-
Can AmbiStack scan barcodes?
Yes, the system can be optionally configured with a variety of scan tunnel solutions. The specific configuration of barcode scanners is based on code type, size, and placement. AmbiStack can also orient package barcodes facing outwards as it builds your pallets.
-
What size cases can it stack?
AmbiStack can palletize cases that weigh a maximum of 50 lbs. Cases can be handled up to 52” long, 32” wide, 32” tall. Palletizing rate and the scan tunnel configurations are affected by the max case size required by each specific application.
-
Can I use AMRs or AGVs to remove full pallet positions?
Yes, AmbiStack is interoperable and ready to integrate with automated robots and vehicles that can remove full pallet locations and bring new pallets to the machine. AmbiStack tracks the completion of all pallet locations, and signals to the pallet moving solution when a pallet position needs to be replenished.
-
How autonomous is AmbiStack? Do I need to do any specific programming or setting up of the solution for different case sizes?
AmbiStack is fully automated, and will palletize cases without any type of customer input required. There are no programs to select from, no programming to do, or any other product specific set up that customers need to worry about.
-
Can AmbiStack palletize my cases in specific patterns that I dictate?
Yes, AmbiStack can follow specific stacking patterns based on product SKU or any other product identifier that can be gathered from the scan tunnel.