IN THE NEWS
Ambi Robotics built a clever solution to automate pallet packing
UC Berkeley spinout Ambi Robotics announced Tuesday the arrival of AmbiStack, a novel system that automates pallet packing.
The system features an industrial robotic arm mounted above a conveyer belt that moves along the X and Y axes and lifts boxes up via suction cups mounted to a gripper. Once lifted from the conveyer belt, the boxes are tightly packed into pallets, which are used to ship or store packages.
The AmbiStack is notable because it combines two key warehouse operations into a single workflow, by both picking and stacking. Both are time-consuming and have been known to cause injury among human workers. Earlier solutions, such as forklifts, have introduced their own injury risk into the workplace. AmbiStack, meanwhile, effectively removes the human worker at these key stages of the logistics process.
Ambi’s solutions focus on both the hardware and software sides of the equation. AmbiStack’s AI offering was trained on more than 200,000 hours of warehouse data, according to the company. That field experience helps the system analyze, track, pick, and place a variety of package sizes.
Presales have already opened for the new system, with the first deployments expected to arrive in mid-2025. Ambi also plans to expand its own manufacturing processes in early-2026 to meet demand.
Ambi was founded in 2018 by UC Berkeley students and lead robotics professor, Ken Goldberg. The firm’s earlier solution, the AmbiSort A-Series, operates in a similar fashion, albeit with smaller parcel packages, which are sorted into bins. That process requires significantly less precision than stacking. The AmbiSort B-Series was released in 2023 with the ability to handle as many as 1,200 sorts in an hour.
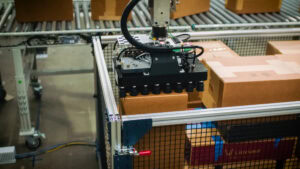
AmbiStack stacking to walled container for maximum utilization.